分析TPM管理对发生源困难点采取对策
来源/作者:未知 发布时间:2014年10月28日 阅读次数:次
一般来说,企业只有把TPM活动的对象从设备扩大到工厂全范围时,才会正式实施针对此类发生源的对策。如果有可能的话,尽量在早期就能明确这种污染源并采取对策是比较理想的。
一、不正常现象与人为劣化
自主保全的第二步是“发生源与困难源的对策”,它的重点是“发现不正常现象,及时进行复原及改善”。为了更好地了解本步骤,我们需要认识什么是“自然劣化”与“人为劣化”。
所谓“自然劣化”,就是由于设备的运动、负荷、时间等物理、化学因素而引起的寿命降低和性能劣化。也就是说,即使人工操作正确,随着设备的使用时间变长,劣化情形仍会持续地发生。而“人为劣化”,就是指使用不当、保养不善、损坏性维修或其他人为原因引起的设备性能降低或寿命降低。由于人为的原因,还可能会导致劣化加速。
当企业发现设备出现不正常现象时,要及时采取“复原”与“改善”措施。所谓“复原”,就是指把已劣化的部分,恢复成原有的正常状态。而“改善”则是指对造成劣化的原因进行分析并采取措施加以解决。
企业以“发现不正常现象,及时进行复原与改善”为重点进行第二步骤时,必须先充分了解人为劣化的原因。否则,便不能采取正确、适当的对策来解决问题。当我们思考人为劣化的原因时,应从“设备及人的行为”两个方面来着手。
首先,从设备方面来谈人为劣化。当我们忽视污染设备发生源的存在时,设备的许多重要部位就会因污染而提早劣化,甚至连清扫或润滑都有困难。其次,从人的行为面上看,由于作业人员不清楚什么是正确的操作程序,导致违反操作规程,于是造成设备劣化加速。
总的来说,“发生源与困难源对策”就是通过对初期清扫遗留下来的难点问题进行分析,再次查找发生源、困难源并实施改善,最终实现以下目标:
1.强化提高在第一阶段“初期清扫”中领会到的“自己的设备自己维护”的思想,并运用到世界的改善活动中去;
2.清除发生源,消除劣化,保持设备清洁;
3.改善困难源,使清扫、润滑等作业简易化,从而达到缩短作业时间的目的;
4.落实清扫、润滑、紧固等作业。
二、发生源与困难源的对策思考
下面,我们先谈谈对于发生源与困难源的整体思考,在后面的章节中再谈一下具体的方法。
1.活动顺序
在某种发生源的清扫有难度的时候,自然会考虑在该部位实施发生源和困难源的对策。
发生源对策包括防止发生对策和防止飞散对策。如果企业能够从源头上防止灰尘或污染的产生,这当然是最好的。如果防止发生对策不成功,或者是实施了防止发生对策后还需要派人定期进行清扫,这时就应该考虑采取防止飞散对策。
如果防止发生对策和防止飞散对策都不成功的话,企业就只能采取困难源对策,即通过改善设备来使清扫变得容易。在困难源对策中,企业应优先考虑改善清扫的顺序或工具,其次才是对设备进行改造,使得清扫变得容易。
2,发生源对策
采取发生源对策,首先考虑的是从根源上防止灰尘、污染的发生,TPM如果不可能做到的话就把发生源控制到极小化使其不到处飞散。灰尘、污染的发生源可以分类为加工原理发生、不正常的发生、设备以外的发生三类。下面,我们按顺序逐个进行说明。
(1)加工原理发生。
即设备在加工原理上必然产生的灰尘、污染。
l切削工序发生的冷却水;
l化学反应的副产物;
l氯代工序产生的氯化氢气体;
这样的发生源谋求以下对策:
l减少:减少切削台、冷却数量,并加上套子来减少溶剂的蒸发;
l控制:不用套子也能防止飞散;
l隔断:用最少的空间影响来防止飞散;
l接:用槽、桶、碟来接。
(2)不正常的发生。
即由于设备管理或维护不当而发生的污染。
l在设备本体上发生泄漏的润滑油、冷却水;
l运转产生的磨损粉;
l从设备落下的制品;
l配管接触部中泄漏的原材料。
针对这种发生源,企业需要的不是减少发生的改善性对策,而是需要从根本上消除发生源的对策。
(3)设备以外的发生。
l粘在抹布和工作用手套上的油渍、线头、头发丝、纤维;
l从厂外搬入的备品、材料商黏着的异物、包装纸、托盘、破损碎片;
l通过工厂棚顶或隔墙侵入的灰尘、虫子。
3.困难源对策
在自主保全活动中,作业人员会找出很多难以清扫的部位。如:
l需要定期清扫的机械,但是没有靠脚的位置或栏杆;
l设计时没有考虑到清扫、点检的需要,因此无法用眼看到也无法用手碰到的地方;
l在设备占地周围密集着管道、电缆、软管等。
针对困难源的改善对策如下:
l把机械移动安全的地方或设置落脚的位置及栏杆;
l设置入口、点检口,对设备进行改善,使其能够拆卸;
l整顿附着的电缆、软管等,按照顺序进行修理。
在困难源对策里,最重要的是设备的操作者自己要有改善的心态。自己发现的问题点尽量自己去处理,但需要焊接、电钻等超过自身能力的工作时,由设备保全部门提供协助。
4.对策的研讨和评价
企业的管理者要经常对各个TPM管理小组进行指导,通过各种改善来提高具体的可视化效果。只靠小范围的改善而不是持之以恒就想获得成就感是不可能的。管理者必须要求全员都养成事前研讨、事后评价的习惯,并灌输全员的成本意识。
5.留下改造记录
图纸是设备情报的重要组织部分,但未必所有的设备改造都画有图纸,所以留下改造记录是非常必要的。如果几年后,企业中没人在知道在什么时间、有什么人、为什么改造设备的话,是无法做到正确的设备管理的。
6.未完成课题的整理
在发生源对策中,我们的目标是挑战于灰尘、污染“0”化。但是,由于各种原因,如订货的备品还没有到货、设备不能停止运行等多种合理的理由,致使一些改善无法顺利进行或是全部完成。也就是说,在现阶段的生产过程中没有办法解决、只能留到以后改善的课题也是会存在的。企业应该对这些遗留下来的课题进行整理,要经常进行再检讨并更新改善计划。
三、污染的根本原因
这里归纳一下,引起设备污染的原因主要有:
l切屑与磨屑到处飞散;
l加工液四处飞溅;
l漏油和垃圾;
l灰尘的附着等。
只要这些情形仍然存在于现场,设备就难以实现在健康状态下长久地运转。
人们之所以会忽略或轻视这些污染,最根本的原因是人们不了解、不知道因自己的忽略或轻视将会给设备带来对坏的影响。也就是说,上至企业领导、管理层,下至作业人员都不认为有防止污染的必要,“防止不防止,机器都会被污染,坏了再修呗”。正是由于抱着这种思想,很多企业根本不去改善因生产加工而对设备造成污染的状态。根据笔者的了解,中国许多企业未去改善设备污染状况的直接原因在于,各级管理人员不了解这些飞散、外漏等情况会给设备带来怎样严重的破坏性。
清洁设备是减少设备不正常现象的基础保证,也是设备不发生人为劣化的先决条件。设备是否处于健康运转状态,与各级人员是否重视设备的污染有关。
四、局部覆盖
通过第一步骤的初期清扫,企业找出了污染对设备造成的不正常现象。好不容易将设备清扫干净,企业自然希望这种干净的状态能够永远保持下去。不过,如果这种干净仅仅只是设备周围干净的话还不行,因为很可能整个设备是被大型的护罩盖住。由于这个大护罩,使得设备内部一旦发生人为劣化的情形,则使清扫、润滑、点检、换模、换线等作业都将变得十分困难。
发现及改善污染发生源是非常重要的,“局部覆盖”是防止飞散对策的重点之一。为了消除发生源,首先尽可能将发生源局限在其本身附近,并以小范围的覆盖防止污染源飞散。
“局部覆盖”的改善方式,可以先从思考开始,如“加工液正确的加入量是多少”、“污染源飞散的方向、角度、数量、速度如何”、“局部覆盖在作业性与安全性上有无问题”等。先从问题的角度进行观察,确认后再着手进行改善。像这样经过思考后再采取对策,即使是极小的覆盖,也能得到较大的改善效果。
下面我们详细说明“局部覆盖”的主要内容:
1.局部化的必要性
现场的设备、机械在工作过程中不断产生切削屑、冲压废边角料等废弃物,尤其是使用湿法加工设备时会产生大量的粉碎、冷却液等,转眼功夫就会把干净的设备弄脏。
所以,一般在脏污较严重的设备上,都可见到覆盖设备全身的、防止飞散的大型套子。这样虽然能够罩住整个机身,但也有它的缺点:
l对机器内部劣化无法进行有效控制,可能导致机械故障;
l不便于清扫、加油、检修作业,难以维护和保养;
l不便于准备及换模工作,准备及换模时间过长。
2.“局部覆盖”的目标
覆盖机械全身的大型套子不但费用高,而且从自主保全的角度来看,清扫碎粉的时间过长也会影响到下一阶段的改善。那么,该怎样去解决这个问题呢?尽量把套子做小(极小化),以及尽可能将飞散物阻止在离发生源近的地方,这就是“局部覆盖”。
通过实施防止飞散局部化,防止污垢、污染物侵入设备的重要功能部位,并且将机器设备从强制劣化中解脱出来,企业会收到以下有形或无形的效果:
l故障发生率大幅降低;
l清扫时间缩短;
l准备及换模时间缩短;
l便于点检切削等;
l便于加油、检修,能够彻底进行保养管理。
3.“局部覆盖”的要点
不同类型的设备,其“局部覆盖”的要点会有所差别。下面以切削粉末及冷却液大量飞散的“湿式加工设备”为例,列举“局部覆盖”局部化的要点。
首先,要看冷却液是否集中在切削点上,若没有集中在切削点上,那不仅将缩短切削刀头的寿命,影响切削效果(表面粗糙度),还会使冷却液四处飞溅。
其次,把握飞散的方向、角度、数量及速度。
最后,确认所制成的局部化套子的形状及大小是否会影响设备的作业性及安全性。
4.进行局部化改善时的注意点
进行局部化改善时,最能准确地掌握从设备中飞散出的切削粉末及冷却液状态的是操作设备的作业人员。因此,在制作局部套子时,决不能完全依赖职能部门的人员,一定要让作业人员参与纸板、白板皮等的手工制作。关键一点就是要利用现场,尤其是TPM管理的小组人员的干劲和技巧。最后,在使用手工制品的过程中,及时对不足之处加以修改,确认没有问题后再以金属板制作。
5.局部化套子的种类
局部化套子从其形状上来讲,可以分为两种。这两种套子都是设备在污染发生源近处,是用来阻止飞散的。
第一种,是用一块或几块板挡住局部发生源,称之为“遮盖板型”套子。这种套子费用不高,而且易于改进。
第二种,是把防止飞散的大型套子进行缩小或局部修改后而成的“箱形”套子,它的费用相对较高,但效果更加令人满意。
局部化套子的制作方法有很多,但都需要现场员工拿出智慧和耐心才能完成。
五、如何缩短清扫时间
我们在看看第二步骤中的“困难源对策”。这里的困难源,包括清扫困难、润滑困难与点检困难,即“操作上很不方便”的部位。常见的清扫、润滑、点检困难部位
1.抑制污染源的扩大
解决清扫困难部位的第一方法是:防止床面的切削液或切屑继续扩大。因为床面污染面积一旦扩大,不但要花更多时间清扫,也会使设备的重要部位受到污染物的侵入。因此,将污染控制在狭小范围,同时让加工产生的切屑随切削液流走是很重要的。如此一来,床面上不但完全没有残留的切屑,而且设备也能经常保清洁的状态。
2.勿将污染物带到不易清扫的地方
解决清扫困难部位的第二方法是不要把污染物带到不易清扫的地方。也就是说在设备不易清扫的部位附近,要防止任何污染的存在。这可使设备的一些重要部位不受污染物侵入。
此外,还有一个方法。那就是将绝对不能受污染的重要部位移至不易受污染的场所。这个方式一旦实行,就不再需要考虑前面两种方法了。但是,这种移动往往需要对设备的构造作深入的研究,这样才能防止设备重要部位的人为劣化。
六、如何缩短加油时间
正确的润滑方式是:视用途将需要的油,适时适量地加入规定的润滑口,并正确供给到摩擦面。不论加油时间多短,都不能忽视上述的润滑条件。
虽然大家都知道润滑的重要性,但每次都要花太多的时间去加油,或是不遵守加油的正确时间。因此,接下来我们要谈谈正确的加油方式,以及如何缩短加油时间。
首先,企业要调查自己的设备有哪些部位需要润滑,加油量是多少。据笔者了解,工厂中多数人虽然都知道哪些部位需要润滑但经常忽略每个部位所需的加油量是各不相同的。
其次,必须注意油的品种的统一。笔者经常发现,许多企业使用的油的黏度虽然相同,但油的制造商却不同,甚至在同一现场还发现了使用黏度不同的油。事实上,不同制造商生产出来的油,一般会有些差别,尽量不要混合使用。因此,为了适用起见,企业必须要求作业人员花时间找出正确的油的种类。一般来说,在现场中只要有3~4中黏度不同的油就足够了。
再次,必须整备储油场所,保管好这些油。例如,必须用干净的容器或加油工具以便供给纯净的油。所以,整备储油场所的目的不是在于方便找油,而是在不出错的情况下保证供给纯净的油。
最后,企业还要重视研究集中加油和自动加油的方式。设备经改善后,虽然缩短了加油时间,但是,加油点过多或仍有加油困难的部位,都是阻碍缩短加油时间的原因。图5-8就是某企业员工自己动手做的一个自动加油装置,数百元的投资换来的是加油时间减少50%。
七、如何缩短点检时间
设备需要点检的部位往往是分散在各处,有时为了点检覆盖在里面的部位或者门中的部位,往往要花不少时间。在此,我们谈一谈如何缩短点检时间的重点。
一般来说,在作业人员的日常点检中,常需用到“五感”,而其中以目视方式最能节省点检时间。
1.将无法看到的点检部位目视化
例如,点检V型皮带时,将皮带覆盖的一小部分以透明PVC(聚氯乙烯)板代替,如此可方便地点检皮带的数目、磨损的状态及污染的程度,甚至作业人员还可以直接打开PVC盖子,检查一下V型皮带的张力。
所以,缩短点检时间的第一个重点就是:将设备的点检项目目视化
2.将仪器、油管油量点检部位集中在与视线等高的设备前面
如果设备的上、下、前、后、左、右,到处都有需要点检的部位,作业人员绕一圈点检可能要花很多的时间。因此,缩短点检时间的第二个重点就是将需要点检的部位(如各种仪表等)集中在与作业人员视线等高处的设备前面,或至少是在同一平面上,以方便点检(见图5-10)。其中,最理想的方式便是像飞机驾驶舱中,所以的仪表仪器都面向飞行员一样,将所有点检的地方都面向作业人员,使他可以很方便地进行各种点检。
3.将无法用眼睛点检的部位进行目视化
例如,为了能及时发现某些关键部位的振动异常时,在合适的位置焊一根铁丝,在铁丝上段的外围再装一个铁丝圈并连接导线。当设备振动异常时,那根铁丝的上段会发生摆动,一旦摆动的振幅较大,“异常”到碰到外围的铁圈时,导线接通,设备上的红色警示灯开始闪烁,作业人员就可以立刻发现振动出现了异常。
再例如,在点检设备内部的马达时,一般人都会打开盖子用手接触,以检查它的振幅和发热的状态,现在,我们可以通过使用振动计和温度计,以目视的方式从设备外部就可以完成点检
免责声明:本文系转载,版权归原作者所有。新益为|精益管理视野鼓励原创行为,本文因转载众多无法找到原作者。如涉及版权,请联系电话023-67015863进行删除!
一、不正常现象与人为劣化
自主保全的第二步是“发生源与困难源的对策”,它的重点是“发现不正常现象,及时进行复原及改善”。为了更好地了解本步骤,我们需要认识什么是“自然劣化”与“人为劣化”。
所谓“自然劣化”,就是由于设备的运动、负荷、时间等物理、化学因素而引起的寿命降低和性能劣化。也就是说,即使人工操作正确,随着设备的使用时间变长,劣化情形仍会持续地发生。而“人为劣化”,就是指使用不当、保养不善、损坏性维修或其他人为原因引起的设备性能降低或寿命降低。由于人为的原因,还可能会导致劣化加速。
当企业发现设备出现不正常现象时,要及时采取“复原”与“改善”措施。所谓“复原”,就是指把已劣化的部分,恢复成原有的正常状态。而“改善”则是指对造成劣化的原因进行分析并采取措施加以解决。
企业以“发现不正常现象,及时进行复原与改善”为重点进行第二步骤时,必须先充分了解人为劣化的原因。否则,便不能采取正确、适当的对策来解决问题。当我们思考人为劣化的原因时,应从“设备及人的行为”两个方面来着手。
首先,从设备方面来谈人为劣化。当我们忽视污染设备发生源的存在时,设备的许多重要部位就会因污染而提早劣化,甚至连清扫或润滑都有困难。其次,从人的行为面上看,由于作业人员不清楚什么是正确的操作程序,导致违反操作规程,于是造成设备劣化加速。
总的来说,“发生源与困难源对策”就是通过对初期清扫遗留下来的难点问题进行分析,再次查找发生源、困难源并实施改善,最终实现以下目标:
1.强化提高在第一阶段“初期清扫”中领会到的“自己的设备自己维护”的思想,并运用到世界的改善活动中去;
2.清除发生源,消除劣化,保持设备清洁;
3.改善困难源,使清扫、润滑等作业简易化,从而达到缩短作业时间的目的;
4.落实清扫、润滑、紧固等作业。
二、发生源与困难源的对策思考
下面,我们先谈谈对于发生源与困难源的整体思考,在后面的章节中再谈一下具体的方法。
1.活动顺序
在某种发生源的清扫有难度的时候,自然会考虑在该部位实施发生源和困难源的对策。
发生源对策包括防止发生对策和防止飞散对策。如果企业能够从源头上防止灰尘或污染的产生,这当然是最好的。如果防止发生对策不成功,或者是实施了防止发生对策后还需要派人定期进行清扫,这时就应该考虑采取防止飞散对策。
如果防止发生对策和防止飞散对策都不成功的话,企业就只能采取困难源对策,即通过改善设备来使清扫变得容易。在困难源对策中,企业应优先考虑改善清扫的顺序或工具,其次才是对设备进行改造,使得清扫变得容易。
2,发生源对策
采取发生源对策,首先考虑的是从根源上防止灰尘、污染的发生,TPM如果不可能做到的话就把发生源控制到极小化使其不到处飞散。灰尘、污染的发生源可以分类为加工原理发生、不正常的发生、设备以外的发生三类。下面,我们按顺序逐个进行说明。
(1)加工原理发生。
即设备在加工原理上必然产生的灰尘、污染。
l切削工序发生的冷却水;
l化学反应的副产物;
l氯代工序产生的氯化氢气体;
这样的发生源谋求以下对策:
l减少:减少切削台、冷却数量,并加上套子来减少溶剂的蒸发;
l控制:不用套子也能防止飞散;
l隔断:用最少的空间影响来防止飞散;
l接:用槽、桶、碟来接。
(2)不正常的发生。
即由于设备管理或维护不当而发生的污染。
l在设备本体上发生泄漏的润滑油、冷却水;
l运转产生的磨损粉;
l从设备落下的制品;
l配管接触部中泄漏的原材料。
针对这种发生源,企业需要的不是减少发生的改善性对策,而是需要从根本上消除发生源的对策。
(3)设备以外的发生。
l粘在抹布和工作用手套上的油渍、线头、头发丝、纤维;
l从厂外搬入的备品、材料商黏着的异物、包装纸、托盘、破损碎片;
l通过工厂棚顶或隔墙侵入的灰尘、虫子。
3.困难源对策
在自主保全活动中,作业人员会找出很多难以清扫的部位。如:
l需要定期清扫的机械,但是没有靠脚的位置或栏杆;
l设计时没有考虑到清扫、点检的需要,因此无法用眼看到也无法用手碰到的地方;
l在设备占地周围密集着管道、电缆、软管等。
针对困难源的改善对策如下:
l把机械移动安全的地方或设置落脚的位置及栏杆;
l设置入口、点检口,对设备进行改善,使其能够拆卸;
l整顿附着的电缆、软管等,按照顺序进行修理。
在困难源对策里,最重要的是设备的操作者自己要有改善的心态。自己发现的问题点尽量自己去处理,但需要焊接、电钻等超过自身能力的工作时,由设备保全部门提供协助。
4.对策的研讨和评价
企业的管理者要经常对各个TPM管理小组进行指导,通过各种改善来提高具体的可视化效果。只靠小范围的改善而不是持之以恒就想获得成就感是不可能的。管理者必须要求全员都养成事前研讨、事后评价的习惯,并灌输全员的成本意识。
5.留下改造记录
图纸是设备情报的重要组织部分,但未必所有的设备改造都画有图纸,所以留下改造记录是非常必要的。如果几年后,企业中没人在知道在什么时间、有什么人、为什么改造设备的话,是无法做到正确的设备管理的。
6.未完成课题的整理
在发生源对策中,我们的目标是挑战于灰尘、污染“0”化。但是,由于各种原因,如订货的备品还没有到货、设备不能停止运行等多种合理的理由,致使一些改善无法顺利进行或是全部完成。也就是说,在现阶段的生产过程中没有办法解决、只能留到以后改善的课题也是会存在的。企业应该对这些遗留下来的课题进行整理,要经常进行再检讨并更新改善计划。
三、污染的根本原因
这里归纳一下,引起设备污染的原因主要有:
l切屑与磨屑到处飞散;
l加工液四处飞溅;
l漏油和垃圾;
l灰尘的附着等。
只要这些情形仍然存在于现场,设备就难以实现在健康状态下长久地运转。
人们之所以会忽略或轻视这些污染,最根本的原因是人们不了解、不知道因自己的忽略或轻视将会给设备带来对坏的影响。也就是说,上至企业领导、管理层,下至作业人员都不认为有防止污染的必要,“防止不防止,机器都会被污染,坏了再修呗”。正是由于抱着这种思想,很多企业根本不去改善因生产加工而对设备造成污染的状态。根据笔者的了解,中国许多企业未去改善设备污染状况的直接原因在于,各级管理人员不了解这些飞散、外漏等情况会给设备带来怎样严重的破坏性。
清洁设备是减少设备不正常现象的基础保证,也是设备不发生人为劣化的先决条件。设备是否处于健康运转状态,与各级人员是否重视设备的污染有关。
四、局部覆盖
通过第一步骤的初期清扫,企业找出了污染对设备造成的不正常现象。好不容易将设备清扫干净,企业自然希望这种干净的状态能够永远保持下去。不过,如果这种干净仅仅只是设备周围干净的话还不行,因为很可能整个设备是被大型的护罩盖住。由于这个大护罩,使得设备内部一旦发生人为劣化的情形,则使清扫、润滑、点检、换模、换线等作业都将变得十分困难。
发现及改善污染发生源是非常重要的,“局部覆盖”是防止飞散对策的重点之一。为了消除发生源,首先尽可能将发生源局限在其本身附近,并以小范围的覆盖防止污染源飞散。
“局部覆盖”的改善方式,可以先从思考开始,如“加工液正确的加入量是多少”、“污染源飞散的方向、角度、数量、速度如何”、“局部覆盖在作业性与安全性上有无问题”等。先从问题的角度进行观察,确认后再着手进行改善。像这样经过思考后再采取对策,即使是极小的覆盖,也能得到较大的改善效果。
下面我们详细说明“局部覆盖”的主要内容:
1.局部化的必要性
现场的设备、机械在工作过程中不断产生切削屑、冲压废边角料等废弃物,尤其是使用湿法加工设备时会产生大量的粉碎、冷却液等,转眼功夫就会把干净的设备弄脏。
所以,一般在脏污较严重的设备上,都可见到覆盖设备全身的、防止飞散的大型套子。这样虽然能够罩住整个机身,但也有它的缺点:
l对机器内部劣化无法进行有效控制,可能导致机械故障;
l不便于清扫、加油、检修作业,难以维护和保养;
l不便于准备及换模工作,准备及换模时间过长。
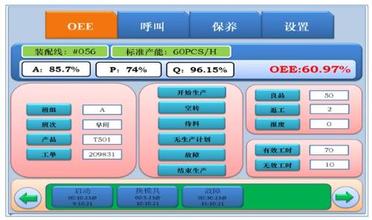
2.“局部覆盖”的目标
覆盖机械全身的大型套子不但费用高,而且从自主保全的角度来看,清扫碎粉的时间过长也会影响到下一阶段的改善。那么,该怎样去解决这个问题呢?尽量把套子做小(极小化),以及尽可能将飞散物阻止在离发生源近的地方,这就是“局部覆盖”。
通过实施防止飞散局部化,防止污垢、污染物侵入设备的重要功能部位,并且将机器设备从强制劣化中解脱出来,企业会收到以下有形或无形的效果:
l故障发生率大幅降低;
l清扫时间缩短;
l准备及换模时间缩短;
l便于点检切削等;
l便于加油、检修,能够彻底进行保养管理。
3.“局部覆盖”的要点
不同类型的设备,其“局部覆盖”的要点会有所差别。下面以切削粉末及冷却液大量飞散的“湿式加工设备”为例,列举“局部覆盖”局部化的要点。
首先,要看冷却液是否集中在切削点上,若没有集中在切削点上,那不仅将缩短切削刀头的寿命,影响切削效果(表面粗糙度),还会使冷却液四处飞溅。
其次,把握飞散的方向、角度、数量及速度。
最后,确认所制成的局部化套子的形状及大小是否会影响设备的作业性及安全性。
4.进行局部化改善时的注意点
进行局部化改善时,最能准确地掌握从设备中飞散出的切削粉末及冷却液状态的是操作设备的作业人员。因此,在制作局部套子时,决不能完全依赖职能部门的人员,一定要让作业人员参与纸板、白板皮等的手工制作。关键一点就是要利用现场,尤其是TPM管理的小组人员的干劲和技巧。最后,在使用手工制品的过程中,及时对不足之处加以修改,确认没有问题后再以金属板制作。
5.局部化套子的种类
局部化套子从其形状上来讲,可以分为两种。这两种套子都是设备在污染发生源近处,是用来阻止飞散的。
第一种,是用一块或几块板挡住局部发生源,称之为“遮盖板型”套子。这种套子费用不高,而且易于改进。
第二种,是把防止飞散的大型套子进行缩小或局部修改后而成的“箱形”套子,它的费用相对较高,但效果更加令人满意。
局部化套子的制作方法有很多,但都需要现场员工拿出智慧和耐心才能完成。
五、如何缩短清扫时间
我们在看看第二步骤中的“困难源对策”。这里的困难源,包括清扫困难、润滑困难与点检困难,即“操作上很不方便”的部位。常见的清扫、润滑、点检困难部位
1.抑制污染源的扩大
解决清扫困难部位的第一方法是:防止床面的切削液或切屑继续扩大。因为床面污染面积一旦扩大,不但要花更多时间清扫,也会使设备的重要部位受到污染物的侵入。因此,将污染控制在狭小范围,同时让加工产生的切屑随切削液流走是很重要的。如此一来,床面上不但完全没有残留的切屑,而且设备也能经常保清洁的状态。
2.勿将污染物带到不易清扫的地方
解决清扫困难部位的第二方法是不要把污染物带到不易清扫的地方。也就是说在设备不易清扫的部位附近,要防止任何污染的存在。这可使设备的一些重要部位不受污染物侵入。
此外,还有一个方法。那就是将绝对不能受污染的重要部位移至不易受污染的场所。这个方式一旦实行,就不再需要考虑前面两种方法了。但是,这种移动往往需要对设备的构造作深入的研究,这样才能防止设备重要部位的人为劣化。
六、如何缩短加油时间
正确的润滑方式是:视用途将需要的油,适时适量地加入规定的润滑口,并正确供给到摩擦面。不论加油时间多短,都不能忽视上述的润滑条件。
虽然大家都知道润滑的重要性,但每次都要花太多的时间去加油,或是不遵守加油的正确时间。因此,接下来我们要谈谈正确的加油方式,以及如何缩短加油时间。
首先,企业要调查自己的设备有哪些部位需要润滑,加油量是多少。据笔者了解,工厂中多数人虽然都知道哪些部位需要润滑但经常忽略每个部位所需的加油量是各不相同的。
其次,必须注意油的品种的统一。笔者经常发现,许多企业使用的油的黏度虽然相同,但油的制造商却不同,甚至在同一现场还发现了使用黏度不同的油。事实上,不同制造商生产出来的油,一般会有些差别,尽量不要混合使用。因此,为了适用起见,企业必须要求作业人员花时间找出正确的油的种类。一般来说,在现场中只要有3~4中黏度不同的油就足够了。
再次,必须整备储油场所,保管好这些油。例如,必须用干净的容器或加油工具以便供给纯净的油。所以,整备储油场所的目的不是在于方便找油,而是在不出错的情况下保证供给纯净的油。
最后,企业还要重视研究集中加油和自动加油的方式。设备经改善后,虽然缩短了加油时间,但是,加油点过多或仍有加油困难的部位,都是阻碍缩短加油时间的原因。图5-8就是某企业员工自己动手做的一个自动加油装置,数百元的投资换来的是加油时间减少50%。
七、如何缩短点检时间
设备需要点检的部位往往是分散在各处,有时为了点检覆盖在里面的部位或者门中的部位,往往要花不少时间。在此,我们谈一谈如何缩短点检时间的重点。
一般来说,在作业人员的日常点检中,常需用到“五感”,而其中以目视方式最能节省点检时间。
1.将无法看到的点检部位目视化
例如,点检V型皮带时,将皮带覆盖的一小部分以透明PVC(聚氯乙烯)板代替,如此可方便地点检皮带的数目、磨损的状态及污染的程度,甚至作业人员还可以直接打开PVC盖子,检查一下V型皮带的张力。
所以,缩短点检时间的第一个重点就是:将设备的点检项目目视化
2.将仪器、油管油量点检部位集中在与视线等高的设备前面
如果设备的上、下、前、后、左、右,到处都有需要点检的部位,作业人员绕一圈点检可能要花很多的时间。因此,缩短点检时间的第二个重点就是将需要点检的部位(如各种仪表等)集中在与作业人员视线等高处的设备前面,或至少是在同一平面上,以方便点检(见图5-10)。其中,最理想的方式便是像飞机驾驶舱中,所以的仪表仪器都面向飞行员一样,将所有点检的地方都面向作业人员,使他可以很方便地进行各种点检。
3.将无法用眼睛点检的部位进行目视化
例如,为了能及时发现某些关键部位的振动异常时,在合适的位置焊一根铁丝,在铁丝上段的外围再装一个铁丝圈并连接导线。当设备振动异常时,那根铁丝的上段会发生摆动,一旦摆动的振幅较大,“异常”到碰到外围的铁圈时,导线接通,设备上的红色警示灯开始闪烁,作业人员就可以立刻发现振动出现了异常。
再例如,在点检设备内部的马达时,一般人都会打开盖子用手接触,以检查它的振幅和发热的状态,现在,我们可以通过使用振动计和温度计,以目视的方式从设备外部就可以完成点检
免责声明:本文系转载,版权归原作者所有。新益为|精益管理视野鼓励原创行为,本文因转载众多无法找到原作者。如涉及版权,请联系电话023-67015863进行删除!