TPEM于TPM管理工作的区别
来源/作者:未知 发布时间:2014年03月18日 阅读次数:次
TPM管理工作是企业的设备管理重点,TPEM工作又是TPM管理工作的衍生,但是他们两者在本质上还是存在着某些差别。
TPEM与TPM的区别
1、什么是TPM?
TPM的提出是建立在美国的生产维修体制的基础上,同时也吸收了英国设备综合工程学、中国鞍钢宪法中里群众参与管理的思想。在非日本国家,由于国情不同,对TPM的理解是:利用包括操作者在内的生产维修活动,提高设备的全面性能。
2、TPEM:
TotalProductiveEquipmentManagement就是全面生产设备管理。这是一种新的维修思想,是由国际TPM协会发展出来的。它是根据非日本文化的特点制定的。使得在一个工厂里安装TPM活动更容易成功一些,和日本的TPM不同的是它的柔性更大一些,也就是说你可根据工厂设备的实际需求来决定开展TPM的内容,也可以说是一种动态的方法。
TPM的特点TPM的特点就是三个“全”,即全效率、全系统和全员参加。
全效率:指设备寿命周期费用评价和设备综合效率。
全系统:指生产维修系统的各个方法都要包括在内。即是PM、MP、CM、BM等都要包含。
全员参加:指设备的计划、使用、维修等所有部门都要参加,尤其注重的是操作者的自主小组活动。
TPM的目标TPM的目标可以概括为四个“零”,即停机为零、废品为零、事故为零、速度损失为零。
停机为零:指计划外的设备停机时间为零。计划外的停机对生产造成冲击相当大,使整个生产品配发生困难,造成资源闲置等浪费。计划时间要有一个合理值,不能为了满足非计划停机为零而使计划停机时间值达到很高。
废品为零:指由设备原因造成的废品为零。“完美的质量需要完善的机器”,机器是保证产品质量的关键,而人是保证机器好坏的关键。
事故为零:指设备运行过程中事故为零。设备事故的危害非常大,影响生产不说,可能会造成人身伤害,严重的可能会“机毁人亡”。
速度损失为零:指设备速度降低造成的产量损失为零。由于设备保养不好,设备精度降低而不能按高速度使用设备,等于降低了设备性能。
推行TPM的要素推行TPM要从三大要素上下功夫,这三大要素是:
1、提高工作技能:不管是操作工,还是设备工程师,都要努力提高工作技能,没有好的工作技能,全员参与将是一句空话。
2、改进精神面貌:精神面貌好,才能形成好的团队,共同促进,共同提高。
3、改善操作环境:通过5S管理等活动,使操作环境良好,一方面可以提高工作兴趣及效率,另一方面可以避免一些不必要设备事故。现场整洁,物料、工具等分门别类摆放,也可使设置调整时间缩短。
免责声明:本文系转载,版权归原作者所有。新益为|精益管理视野鼓励原创行为,本文因转载众多无法找到原作者。如涉及版权,请联系电话023-67015863进行删除!
TPEM与TPM的区别
1、什么是TPM?
TPM的提出是建立在美国的生产维修体制的基础上,同时也吸收了英国设备综合工程学、中国鞍钢宪法中里群众参与管理的思想。在非日本国家,由于国情不同,对TPM的理解是:利用包括操作者在内的生产维修活动,提高设备的全面性能。
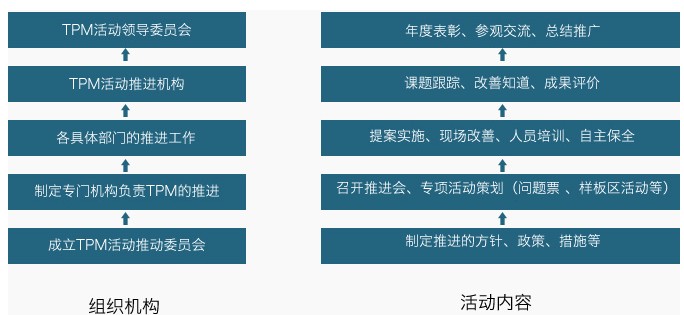
TotalProductiveEquipmentManagement就是全面生产设备管理。这是一种新的维修思想,是由国际TPM协会发展出来的。它是根据非日本文化的特点制定的。使得在一个工厂里安装TPM活动更容易成功一些,和日本的TPM不同的是它的柔性更大一些,也就是说你可根据工厂设备的实际需求来决定开展TPM的内容,也可以说是一种动态的方法。
TPM的特点TPM的特点就是三个“全”,即全效率、全系统和全员参加。
全效率:指设备寿命周期费用评价和设备综合效率。
全系统:指生产维修系统的各个方法都要包括在内。即是PM、MP、CM、BM等都要包含。
全员参加:指设备的计划、使用、维修等所有部门都要参加,尤其注重的是操作者的自主小组活动。
TPM的目标TPM的目标可以概括为四个“零”,即停机为零、废品为零、事故为零、速度损失为零。
停机为零:指计划外的设备停机时间为零。计划外的停机对生产造成冲击相当大,使整个生产品配发生困难,造成资源闲置等浪费。计划时间要有一个合理值,不能为了满足非计划停机为零而使计划停机时间值达到很高。
废品为零:指由设备原因造成的废品为零。“完美的质量需要完善的机器”,机器是保证产品质量的关键,而人是保证机器好坏的关键。
事故为零:指设备运行过程中事故为零。设备事故的危害非常大,影响生产不说,可能会造成人身伤害,严重的可能会“机毁人亡”。
速度损失为零:指设备速度降低造成的产量损失为零。由于设备保养不好,设备精度降低而不能按高速度使用设备,等于降低了设备性能。
推行TPM的要素推行TPM要从三大要素上下功夫,这三大要素是:
1、提高工作技能:不管是操作工,还是设备工程师,都要努力提高工作技能,没有好的工作技能,全员参与将是一句空话。
2、改进精神面貌:精神面貌好,才能形成好的团队,共同促进,共同提高。
3、改善操作环境:通过5S管理等活动,使操作环境良好,一方面可以提高工作兴趣及效率,另一方面可以避免一些不必要设备事故。现场整洁,物料、工具等分门别类摆放,也可使设置调整时间缩短。
免责声明:本文系转载,版权归原作者所有。新益为|精益管理视野鼓励原创行为,本文因转载众多无法找到原作者。如涉及版权,请联系电话023-67015863进行删除!