精益生产方式目标和方法体系之间的关联
来源/作者:未知 发布时间:2014年05月29日 阅读次数:次
精益生产方式作为一种生产管理技术,是各种思想和方法的集合,并且这些思想和方法都是从各个方面来实现其基本目标的。因此,精益生产方式具有一种反映其目标←→方法关系的体系。在这个体系中,包括精益生产方式的基本目标以及实现这些目标的多种方法,也包括这些目标与各种方法之间的相互内在联系。
一、精益生产方式的目标
精益生产方式的最终目标即企业的经营目的是获取利润。为了实现这个最终目标,“降低成本”就成为基本目标。如前所述,在福特时代,降低成本主要是依靠单一品种的规模生产来实现的。日本在20世纪60年代以及70年代初的经济高度成长期,由于需求不断增加,采取大批量生产也取得了良好的效果。在这样的情况下,实际上不需要太严密的生产计划和细致的管理,即使出现生产日程频繁变动、工序间在制品库存不断增加、间接作业工时过大等问题,只要能保证质量,企业便可放开手大量生产,确保企业利润就不成问题。但是在多品种小批量生产的情况下,这一方法是行不通的。因此,精益生产方式力图通过“彻底排除浪费”来达到这一目标。
所谓浪费,在精益生产方式的起源地丰田汽车公司,被定义为“只使成本增加的生产诸因素”,也就是说,不会带来任何附加价值的诸因素。这其中,最主要的有生产过剩(即库存)所引起的浪费,人员利用上的浪费以及不合格产品所引起的浪费。因此,为了排除这些浪费,就相应地产生了适时适量生产、弹性配置作业人数以及保证质量这样的课题。这些课题成为降低成本这一基本目标的子目标。
二、精益生产方式的基本方法
为了达到降低成本这一基本目标,对应于上述这一基本目标的三个子目标,精益生产方式的基本方法也可以概括为下述三个方面:
1、适时适量生产。即“JustInTime”本来所要表达的含义--“在需要的时候,按需要的量生产所需的产品”。当今的时代已经从“只要生产得出来就卖得出去”进入了一个“只能生产能够卖得出去的产品”的时代,对于企业来说,各种产品的产量必须能够灵活地适应市场需求的变化。否则的话,由于生产过剩会引起人员、设备、库存费用等一系列的浪费。而避免这些浪费的方法就是实施适时适量生产,只在市场需要的时候生产市场需要的产品。精益的这种思想与历来的有关生产及库存的观念截然不同。
2、弹性配置作业人数。在劳动费用越来越高的今天,降低劳动费用是降低成本的一个重要方面。达到这一目的的方法是“少人化”。所谓少人化,是指根据生产量的变动,弹性地增减各生产线的作业人数,以及尽量用较少的人力完成较多的生产。这里的关键在于能否将生产量减少了的生产线上的作业人员数减下来。这种“少人化”技术一反历来的生产系统中的“定员制”,是一种全新的人员配置方法。
实现这种少人化的具体方法是实施独特的设备布置,以便能够将需求减少时各作业点减少的工作集中起来,以整数削减人员。但这从作业人员的角度来看,意味着标准作业时间、作业内容、范围、作业组合以及作业顺序等的一系列变更。因此为了适应这种变更,作业人员必须是具有多种机能的“多面手”。
3、雇员保证。历来认为,质量与成本之间是一种负相关关系,即要提高质量,就得花人力、物力来加以保证。但在精益生产方式中,却一反这一常识,通过将质量管理贯穿于每一工序之中来实现提高质量与降低成本的一致性,具体方法是“自动化”。这里所讲的“自动化”,不是一般意义上的设备、监控系统的自动化,而是指融入生产组织中的这样两种机制:第一,使设备或生产线能够自动监测不良产品,一旦发现异常或不良产品,可以自动停止的设备运行机制。为此在设备上开发、安装了各种自动停止装置和加工状态监测装置;第二,生产第一线的设备操作工人发现产品和设备的问题时,有权自动停止生产的管理机制。依靠这样的机制,不良产品一出现马上就会被发现,防止了不良产品的重复出现或累计出现,从而避免了由此可能造成的大量浪费。而且,由于一旦发生异常,生产线或设备就立即停止运行,比较容易找到异常的原因,从而能够针对性地采取措施,防止类似异常情况的再发生,杜绝类似不良品的再产生。
这里还值得一提的是,通常的质量管理方法,是在最后一道工序对产品进行检验,如有不合格进行返工或作其他处理,而尽量不让生产线或加工中途停止。但在精益生产管理中,却认为这恰恰是使不良产品大量或重复出现的“元凶”。因为发现问题后不立即停止生产的话,问题就得不到暴露,以后难免还会出现类似的问题。而一旦发现问题就使其停止,并立即对其进行分析、改善的话,久而久之,生产中存在的问题就会越来越少,企业的生产素质就会逐渐增强。
三、实现适时适量生产的具体手法
实现适时适量生产的具体手法包括以下一些:
1、生产同步化。为了实现适时适量生产,首先需要致力于生产的同步化。即工序间不设置仓库,前一工序的加工结束后,使其立即转到下一工序去,装配线与机加工几乎平行运行,产品被一件一件、连续地生产出来。在铸造、锻造、冲压等必须成批生产的工序,则通过尽量缩短作业更换时间来尽量缩小生产批量。
生产的同步化通过“后工序领取”这样的方法来实现。即“后工序只在需要的时候到前工序领取所需的加工品;前工序只按照被领取走的数量和品种进行生产”。这样,制造工序的最后一道,即总装配线成为生产的出发点,生产计划只下达给总装配线,以装配为起点,在需要的时候,向前工序领取必要的工件,而前工序提供该工件后,为了补充生产被领取走的量,必然会向更前一道工序去领取所需的零部件,。这样一层一层向前工序领取,直至粗加工以及原材料部门,把各个工序都连接起来。
这样的同步化生产还需要通过采取相应的设备配置方法和人员配置方法来实现。即与通常机械厂中所采用的按照车、铣、刨等工艺对象专业化的生产组织方式不同,采取产品对象专业化的组织形式,按照工件加工顺序来布置设备。这样也带来人员配置上的不同做法。
2、生产均衡化。生产均衡化是实现适时适量生产的前提条件。所谓生产均衡化,是指总装配线在向前工序领取零部件时,应均衡地使用各种零部件,混合生产各种产品。为此在制定生产计划时就必须加以考虑,然后将其体现于产品投产顺序计划之中。在制造阶段,均衡化通过专用设备通用化和制定标准作业来实现。所谓专业设备通用化,是指通过在专用设备上增加一些工夹具等方法,使之能够加工多种不同的产品。标准作业是指将作业节拍内一个作业人员所应担当的一系列作业内容标准化。
3、实现适时适量生产的管理工具。在实现适时适量生产中具有极为重要意义的是作为其管理工具的看板。看板管理也可以说是精益生产方式中最独特的部分,因此也有人将精益生产方式称为“看班方式”。但是严格地讲,这种概念是不正确的。因为如前所述,精益生产方式的本质,是一种生产管理技术,而看板只不过是一种管理工具。
看板的主要机能是传递生产和运送的指令。在精益生产方式中,生产的月度计划是集中制定的,同时传达到各个工厂以及协作企业。而与此相对应的日生产指令只下达到最后一道工序或总装配线,对其它工序的生产指令均通过看板来实现。即后工序“在需要的时候”用看板向前工序去领取“所需的量”时,同时就向前工序发出了生产指令。由于生产量是不可能完全按照计划进行的,日生产量以及日生产计划的修改都通过看板来进行微调。看板就相当于工序之间、部门之间以及物流之间的联络神经而发挥着作用。
免责声明:本文系转载,版权归原作者所有。新益为|精益管理视野鼓励原创行为,本文因转载众多无法找到原作者。如涉及版权,请联系电话023-67015863进行删除!
一、精益生产方式的目标
精益生产方式的最终目标即企业的经营目的是获取利润。为了实现这个最终目标,“降低成本”就成为基本目标。如前所述,在福特时代,降低成本主要是依靠单一品种的规模生产来实现的。日本在20世纪60年代以及70年代初的经济高度成长期,由于需求不断增加,采取大批量生产也取得了良好的效果。在这样的情况下,实际上不需要太严密的生产计划和细致的管理,即使出现生产日程频繁变动、工序间在制品库存不断增加、间接作业工时过大等问题,只要能保证质量,企业便可放开手大量生产,确保企业利润就不成问题。但是在多品种小批量生产的情况下,这一方法是行不通的。因此,精益生产方式力图通过“彻底排除浪费”来达到这一目标。
所谓浪费,在精益生产方式的起源地丰田汽车公司,被定义为“只使成本增加的生产诸因素”,也就是说,不会带来任何附加价值的诸因素。这其中,最主要的有生产过剩(即库存)所引起的浪费,人员利用上的浪费以及不合格产品所引起的浪费。因此,为了排除这些浪费,就相应地产生了适时适量生产、弹性配置作业人数以及保证质量这样的课题。这些课题成为降低成本这一基本目标的子目标。
二、精益生产方式的基本方法
为了达到降低成本这一基本目标,对应于上述这一基本目标的三个子目标,精益生产方式的基本方法也可以概括为下述三个方面:
1、适时适量生产。即“JustInTime”本来所要表达的含义--“在需要的时候,按需要的量生产所需的产品”。当今的时代已经从“只要生产得出来就卖得出去”进入了一个“只能生产能够卖得出去的产品”的时代,对于企业来说,各种产品的产量必须能够灵活地适应市场需求的变化。否则的话,由于生产过剩会引起人员、设备、库存费用等一系列的浪费。而避免这些浪费的方法就是实施适时适量生产,只在市场需要的时候生产市场需要的产品。精益的这种思想与历来的有关生产及库存的观念截然不同。
2、弹性配置作业人数。在劳动费用越来越高的今天,降低劳动费用是降低成本的一个重要方面。达到这一目的的方法是“少人化”。所谓少人化,是指根据生产量的变动,弹性地增减各生产线的作业人数,以及尽量用较少的人力完成较多的生产。这里的关键在于能否将生产量减少了的生产线上的作业人员数减下来。这种“少人化”技术一反历来的生产系统中的“定员制”,是一种全新的人员配置方法。
实现这种少人化的具体方法是实施独特的设备布置,以便能够将需求减少时各作业点减少的工作集中起来,以整数削减人员。但这从作业人员的角度来看,意味着标准作业时间、作业内容、范围、作业组合以及作业顺序等的一系列变更。因此为了适应这种变更,作业人员必须是具有多种机能的“多面手”。
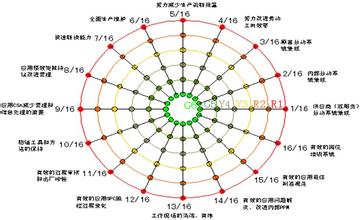
3、雇员保证。历来认为,质量与成本之间是一种负相关关系,即要提高质量,就得花人力、物力来加以保证。但在精益生产方式中,却一反这一常识,通过将质量管理贯穿于每一工序之中来实现提高质量与降低成本的一致性,具体方法是“自动化”。这里所讲的“自动化”,不是一般意义上的设备、监控系统的自动化,而是指融入生产组织中的这样两种机制:第一,使设备或生产线能够自动监测不良产品,一旦发现异常或不良产品,可以自动停止的设备运行机制。为此在设备上开发、安装了各种自动停止装置和加工状态监测装置;第二,生产第一线的设备操作工人发现产品和设备的问题时,有权自动停止生产的管理机制。依靠这样的机制,不良产品一出现马上就会被发现,防止了不良产品的重复出现或累计出现,从而避免了由此可能造成的大量浪费。而且,由于一旦发生异常,生产线或设备就立即停止运行,比较容易找到异常的原因,从而能够针对性地采取措施,防止类似异常情况的再发生,杜绝类似不良品的再产生。
这里还值得一提的是,通常的质量管理方法,是在最后一道工序对产品进行检验,如有不合格进行返工或作其他处理,而尽量不让生产线或加工中途停止。但在精益生产管理中,却认为这恰恰是使不良产品大量或重复出现的“元凶”。因为发现问题后不立即停止生产的话,问题就得不到暴露,以后难免还会出现类似的问题。而一旦发现问题就使其停止,并立即对其进行分析、改善的话,久而久之,生产中存在的问题就会越来越少,企业的生产素质就会逐渐增强。
三、实现适时适量生产的具体手法
实现适时适量生产的具体手法包括以下一些:
1、生产同步化。为了实现适时适量生产,首先需要致力于生产的同步化。即工序间不设置仓库,前一工序的加工结束后,使其立即转到下一工序去,装配线与机加工几乎平行运行,产品被一件一件、连续地生产出来。在铸造、锻造、冲压等必须成批生产的工序,则通过尽量缩短作业更换时间来尽量缩小生产批量。
生产的同步化通过“后工序领取”这样的方法来实现。即“后工序只在需要的时候到前工序领取所需的加工品;前工序只按照被领取走的数量和品种进行生产”。这样,制造工序的最后一道,即总装配线成为生产的出发点,生产计划只下达给总装配线,以装配为起点,在需要的时候,向前工序领取必要的工件,而前工序提供该工件后,为了补充生产被领取走的量,必然会向更前一道工序去领取所需的零部件,。这样一层一层向前工序领取,直至粗加工以及原材料部门,把各个工序都连接起来。
这样的同步化生产还需要通过采取相应的设备配置方法和人员配置方法来实现。即与通常机械厂中所采用的按照车、铣、刨等工艺对象专业化的生产组织方式不同,采取产品对象专业化的组织形式,按照工件加工顺序来布置设备。这样也带来人员配置上的不同做法。
2、生产均衡化。生产均衡化是实现适时适量生产的前提条件。所谓生产均衡化,是指总装配线在向前工序领取零部件时,应均衡地使用各种零部件,混合生产各种产品。为此在制定生产计划时就必须加以考虑,然后将其体现于产品投产顺序计划之中。在制造阶段,均衡化通过专用设备通用化和制定标准作业来实现。所谓专业设备通用化,是指通过在专用设备上增加一些工夹具等方法,使之能够加工多种不同的产品。标准作业是指将作业节拍内一个作业人员所应担当的一系列作业内容标准化。
3、实现适时适量生产的管理工具。在实现适时适量生产中具有极为重要意义的是作为其管理工具的看板。看板管理也可以说是精益生产方式中最独特的部分,因此也有人将精益生产方式称为“看班方式”。但是严格地讲,这种概念是不正确的。因为如前所述,精益生产方式的本质,是一种生产管理技术,而看板只不过是一种管理工具。
看板的主要机能是传递生产和运送的指令。在精益生产方式中,生产的月度计划是集中制定的,同时传达到各个工厂以及协作企业。而与此相对应的日生产指令只下达到最后一道工序或总装配线,对其它工序的生产指令均通过看板来实现。即后工序“在需要的时候”用看板向前工序去领取“所需的量”时,同时就向前工序发出了生产指令。由于生产量是不可能完全按照计划进行的,日生产量以及日生产计划的修改都通过看板来进行微调。看板就相当于工序之间、部门之间以及物流之间的联络神经而发挥着作用。
免责声明:本文系转载,版权归原作者所有。新益为|精益管理视野鼓励原创行为,本文因转载众多无法找到原作者。如涉及版权,请联系电话023-67015863进行删除!