分析TPM管理推进中五个为什么
来源/作者:未知 发布时间:2014年08月28日 阅读次数:次
TPM小组活动在各个阶段有所侧重。TPM管理实施的初期,以清洁、培训为主;中期以维修操作为主;后期以小组会议、检查和自主维修为主。企业的管理人员从步骤6起就有计划地引导小组活动。从步骤7起,工人就应能够独立、自主地进行维修。
模具厂早已提出要求,对品质异常要“问5个为什么?”,但效果并不太好。在《丰田生产方式》看到这一段,请大家思考:
你对一个现象提过五个“为什么”吗?说起来容易,TPM管理做起来可就难了。
比如说,假定机器开不动了:
(1)“为什么机器停了?”“因为负荷过大,保险丝断了。”
(2)“为什么会负荷过大?”“因为轴承部分不够润滑。”
(3)“为什么不够润滑?”“因为润滑油泵吸不上来。”
(4)“为什么吸不上来?”“因为油泵轴磨损,松动了。”
(5)“为什么磨损了?”“因为没有安装过滤器,粉屑进去了。”
反复上述五个“为什么”就会发现需要安装过滤器。
如果“为什么”没有问到底,换上保险丝或换上油泵轴就了事,那么,几个月后就会再次发生这样的事。
说实在的,丰田生产方式也不妨说是丰田人反复问“为什么”,积累并发扬科学的认识态度,才创造出来的。
自问自答这五个“为什么”,就可以查明事情的因果关系或隐藏在背后的真实原因。
“为什么丰田汽车工业公司里,一个人只能管一台机器?”
提出这个问题,就得到解答:“因为机器不是加工完毕就停转的。”由此得到启发,便产生了“自动化”的想法。
“为什么不能非常准时的生产呢?”提出这个问题,便会得到例如说“前一道工序出得太快太多。不知道造出一个要几分钟”的回答。于是得到了启发,便产生了“均匀化”的想法。
“为什么发生过量制造的浪费?”对这个问题,于是就引出了5S管理内容中的“目视管理”,进而引出了“传票卡”的想法。
就生产现场而言,我当然是重视数据的,但是我最重视事实。一旦发生问题,如果原因追查不彻底,解决方法也就不对头。因此,我就反复提出五个“为什么”。这构成了丰田式的科学态度的基本精神。
免责声明:本文系转载,版权归原作者所有。新益为|精益管理视野鼓励原创行为,本文因转载众多无法找到原作者。如涉及版权,请联系电话023-67015863进行删除!
模具厂早已提出要求,对品质异常要“问5个为什么?”,但效果并不太好。在《丰田生产方式》看到这一段,请大家思考:
你对一个现象提过五个“为什么”吗?说起来容易,TPM管理做起来可就难了。
比如说,假定机器开不动了:
(1)“为什么机器停了?”“因为负荷过大,保险丝断了。”
(2)“为什么会负荷过大?”“因为轴承部分不够润滑。”
(3)“为什么不够润滑?”“因为润滑油泵吸不上来。”
(4)“为什么吸不上来?”“因为油泵轴磨损,松动了。”
(5)“为什么磨损了?”“因为没有安装过滤器,粉屑进去了。”
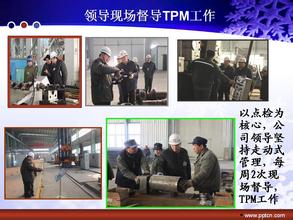
如果“为什么”没有问到底,换上保险丝或换上油泵轴就了事,那么,几个月后就会再次发生这样的事。
说实在的,丰田生产方式也不妨说是丰田人反复问“为什么”,积累并发扬科学的认识态度,才创造出来的。
自问自答这五个“为什么”,就可以查明事情的因果关系或隐藏在背后的真实原因。
“为什么丰田汽车工业公司里,一个人只能管一台机器?”
提出这个问题,就得到解答:“因为机器不是加工完毕就停转的。”由此得到启发,便产生了“自动化”的想法。
“为什么不能非常准时的生产呢?”提出这个问题,便会得到例如说“前一道工序出得太快太多。不知道造出一个要几分钟”的回答。于是得到了启发,便产生了“均匀化”的想法。
“为什么发生过量制造的浪费?”对这个问题,于是就引出了5S管理内容中的“目视管理”,进而引出了“传票卡”的想法。
就生产现场而言,我当然是重视数据的,但是我最重视事实。一旦发生问题,如果原因追查不彻底,解决方法也就不对头。因此,我就反复提出五个“为什么”。这构成了丰田式的科学态度的基本精神。
免责声明:本文系转载,版权归原作者所有。新益为|精益管理视野鼓励原创行为,本文因转载众多无法找到原作者。如涉及版权,请联系电话023-67015863进行删除!