6S管理对企业TPM管理的重要意义
来源/作者:未知 发布时间:2013年12月04日 阅读次数:次
TPM设备管理处在企业的工作现场。6S管理工作也以企业现场管理工作为重点,在企业中TPM设备管理工作中加入6S管理工作,是做好企业的TPM管理工作的重点。
6S活动对TPM设备管理的重要意义企业最本质、最重要、最基础的工作是在现场,通过推行6S管理——整理、整顿、清洁、素养、规范和安全,逐步深化现场管理,改善工作环境,提高工作效率,提高员工素质,确保安全生产,保证产品质量。从现场管理讲,设备可同时列为“污染源、清扫困难源、故障源、浪费源、缺陷源和危险源”(以下简称“6源”),因此,做好6S管理,TPM管理是一个重要方面。开展TPM管理工作要从规范设备工作环境,预防和消除“6源”,规范设备现场的日常维护,建立健全规范的TPM管理制度,提高职工素质,以及建立考核体制方面开展工作。
一、规范设备工作环境
根据设备特点和使用要求,建立或配制设备特殊工艺条件要求的环境设施,满足对温度、洁净度等的要求,整理和整顿好设备的工作环境和设备附件,认真区分工作场所要与不要的物品。通过将不需要的物品处理掉,让生产现场和工作场所透明化,增大作业空间,减少碰撞事故,提高工作效率。并把留下有用的东西加以定置、定位,按照使用频率和可视化准则,合理布置摆放,做到规范化、色彩标记化和定置化,从而做好企业的TPM管理工作。
二、查找和设备有关的“6源”,也是企业TPM管理工作的重点之一。
(1)查污染源。污染源指由设备引起的灰尘、油污、废料、加工材屑等,更深的包括有害气体、有毒液体、电磁辐射、光辐射以及噪声方面的污染。寻找、搜集这些污染源的信息后,通过源头控制、采取防护措施等办法加以解决。
(2)查清扫困难源。清扫困难源指设备难以清扫的部位,包括空间狭窄、没人工作的部位、设备内部深层无法使用清扫工具的部位;污染频繁,无法随时清扫的部位;人员难以接近的区域,如高空、高温、设备高速运转部分等。
(3)查危险源。危险源是指和设备有关的安全事故发生源。由于设备向大型、连续化方向发展,一旦出了事故,可能给企业乃至社会带来危害。安全工作必须做到“预防为主、防微杜渐、防患于未然”,必须消除可能由设备引发的事故和事故苗头,要积极寻找安全隐患并制定策略,如检查设备的各种安全装置是否齐全可靠,设备使用的元器件是否符合国家有关规定,设备的使用维护修理规范是否符合安全要求等。对特种设备,如输变电设备、压力容器等设备,要严格按照国家的有关规定和技术标准,由有资质的单位进行定期检查和修理。
(4)查浪费源。浪费源指和设备相关的各种能源浪费,这也是开展好TPM管理工作要点之一。第一类浪费是“跑、冒、滴、漏”,包括漏水、漏油、漏电、漏气(汽)以及各种生产用介质等的泄漏(这些泄漏也可污染环境);第二类是“开关”方面的浪费,如人走灯还亮,机器空运转,冷气、热风、风扇等方面的能源浪费等。要采用各种技术手段做好防漏、堵漏工作,要通过开关处提示,以及员工良好习惯来杜绝浪费。
(5)查故障源。故障源指设备自身故障。要通过日常的统计分析,逐步了解掌握设备故障发生的原因和规律,制定相应的措施以延长设备正常运转时间,如因润滑不良造成故障,采取加强改造润滑系统;因温度高、散热差引起的故障,通过加强冷风机或冷却水来实现等。
(6)查缺陷源。缺陷源指现有设备不能满足产品质量要求的方面。围绕保障和提高产品质量,寻找影响产品质量的加工环节,并通过对现有的设备进行技术改造和更新来实现。
通过对查出的“6源”分门别类采取相应的措施,实现消除、降低和预防“6源”。
三、编制完善的TPM现场工作规范
在编制日常工作规范时,要组织技术骨干,包括设备部门、车间、维护组、一线生产技术骨干选择典型机台、生产线、典型管理过程进行攻关,调查研究、摸清规律、进行试验,通过“选人、选点、选项、选时、选标、选法、选班、选路”,制定适合设备现状的设备操作、清扫、点检、保养和润滑规范,确定工作流程,制定出科学合理的规范,并逐步推广到企业所有机台和管理过程,最终达到台台设备及各个环节都有规范。
TPM管理工作是企业共组的重点,也是企业发展的难点。
免责声明:本文系转载,版权归原作者所有。新益为|精益管理视野鼓励原创行为,本文因转载众多无法找到原作者。如涉及版权,请联系电话023-67015863进行删除!
6S活动对TPM设备管理的重要意义企业最本质、最重要、最基础的工作是在现场,通过推行6S管理——整理、整顿、清洁、素养、规范和安全,逐步深化现场管理,改善工作环境,提高工作效率,提高员工素质,确保安全生产,保证产品质量。从现场管理讲,设备可同时列为“污染源、清扫困难源、故障源、浪费源、缺陷源和危险源”(以下简称“6源”),因此,做好6S管理,TPM管理是一个重要方面。开展TPM管理工作要从规范设备工作环境,预防和消除“6源”,规范设备现场的日常维护,建立健全规范的TPM管理制度,提高职工素质,以及建立考核体制方面开展工作。
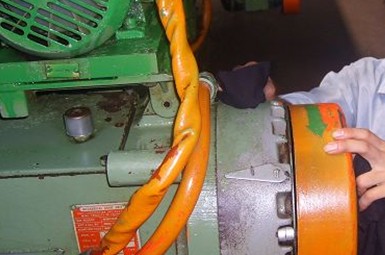
根据设备特点和使用要求,建立或配制设备特殊工艺条件要求的环境设施,满足对温度、洁净度等的要求,整理和整顿好设备的工作环境和设备附件,认真区分工作场所要与不要的物品。通过将不需要的物品处理掉,让生产现场和工作场所透明化,增大作业空间,减少碰撞事故,提高工作效率。并把留下有用的东西加以定置、定位,按照使用频率和可视化准则,合理布置摆放,做到规范化、色彩标记化和定置化,从而做好企业的TPM管理工作。
二、查找和设备有关的“6源”,也是企业TPM管理工作的重点之一。
(1)查污染源。污染源指由设备引起的灰尘、油污、废料、加工材屑等,更深的包括有害气体、有毒液体、电磁辐射、光辐射以及噪声方面的污染。寻找、搜集这些污染源的信息后,通过源头控制、采取防护措施等办法加以解决。
(2)查清扫困难源。清扫困难源指设备难以清扫的部位,包括空间狭窄、没人工作的部位、设备内部深层无法使用清扫工具的部位;污染频繁,无法随时清扫的部位;人员难以接近的区域,如高空、高温、设备高速运转部分等。
(3)查危险源。危险源是指和设备有关的安全事故发生源。由于设备向大型、连续化方向发展,一旦出了事故,可能给企业乃至社会带来危害。安全工作必须做到“预防为主、防微杜渐、防患于未然”,必须消除可能由设备引发的事故和事故苗头,要积极寻找安全隐患并制定策略,如检查设备的各种安全装置是否齐全可靠,设备使用的元器件是否符合国家有关规定,设备的使用维护修理规范是否符合安全要求等。对特种设备,如输变电设备、压力容器等设备,要严格按照国家的有关规定和技术标准,由有资质的单位进行定期检查和修理。
(4)查浪费源。浪费源指和设备相关的各种能源浪费,这也是开展好TPM管理工作要点之一。第一类浪费是“跑、冒、滴、漏”,包括漏水、漏油、漏电、漏气(汽)以及各种生产用介质等的泄漏(这些泄漏也可污染环境);第二类是“开关”方面的浪费,如人走灯还亮,机器空运转,冷气、热风、风扇等方面的能源浪费等。要采用各种技术手段做好防漏、堵漏工作,要通过开关处提示,以及员工良好习惯来杜绝浪费。
(5)查故障源。故障源指设备自身故障。要通过日常的统计分析,逐步了解掌握设备故障发生的原因和规律,制定相应的措施以延长设备正常运转时间,如因润滑不良造成故障,采取加强改造润滑系统;因温度高、散热差引起的故障,通过加强冷风机或冷却水来实现等。
(6)查缺陷源。缺陷源指现有设备不能满足产品质量要求的方面。围绕保障和提高产品质量,寻找影响产品质量的加工环节,并通过对现有的设备进行技术改造和更新来实现。
通过对查出的“6源”分门别类采取相应的措施,实现消除、降低和预防“6源”。
三、编制完善的TPM现场工作规范
在编制日常工作规范时,要组织技术骨干,包括设备部门、车间、维护组、一线生产技术骨干选择典型机台、生产线、典型管理过程进行攻关,调查研究、摸清规律、进行试验,通过“选人、选点、选项、选时、选标、选法、选班、选路”,制定适合设备现状的设备操作、清扫、点检、保养和润滑规范,确定工作流程,制定出科学合理的规范,并逐步推广到企业所有机台和管理过程,最终达到台台设备及各个环节都有规范。
TPM管理工作是企业共组的重点,也是企业发展的难点。
免责声明:本文系转载,版权归原作者所有。新益为|精益管理视野鼓励原创行为,本文因转载众多无法找到原作者。如涉及版权,请联系电话023-67015863进行删除!