如何进行工厂5S管理现场改善
来源/作者:未知 发布时间:2014年06月04日 阅读次数:次
5S管理活动从改善着手。在改善的范畴里,管理具有两项主要的功能:“维持”(Maintenance)与“改进”(Improvement)。“维持”是指从事于保持现有技术、管理及作业上标准的活动,以及支持这些标准所需的训练和纪律。在“维持”的功能下,管理部门要执行工作的指派,使每一个人都能依照标准的作业程序来工作;而“改进”则是以改进现有标准为目标的活动。日本的管理观点,因此可以浓缩为一句箴言来表示:维持标准和改进标准。
改进可再区分为“改善”(Kaizen)和“创新”(Innovation)。所谓“改善”,是由于持续不断的努力,所产生的诸多的小步伐改进,而逐次累积而成。“创新”则是借助大笔资源投资于新技术或设备,而产生戏剧性的变化的改进(不论任何场合,以金钱作为主要的评估因素时,创新便是昂贵的)。由于欧美的管理人员执迷于“创新”,他们既没有耐心,也忽视了“改善”能长期带给公司的利益。相反,“改善”则是强调要以员工的努力、士气、沟通、训练、团队、参与及5S培训自律来达成目标。这些都是一种常识性和低成本的改进方式。
“改善”是着重在“过程为导向”的思考模式上,这是因为要改进“结果”,必须先改进“过程”。预期的计划成果未能达成,表示其“过程”是失败的。管理部门必须确认及改正这种“过程面”的错误。“改善”是着重在“人际面”上的努力,此种东方的改善形态,恰与西方的着重在“结果面”的思想,形成尖锐的对比。以“过程为导向”的思想方式,应当运用在各种不同的改善活动上,诸如:计划→执行→核查→处置(PDCA)的循环、标准化→执行→核查→处置(SDCA)的循环、质量→成本→交期(QCD)的活动、全面质量管理(TQM)及时生产方式(JIT)和全员生产保全(TPM)。许多公司改善活动失败的原因,就在于轻忽“过程”。在“改善”的过程中,最关键性的就是最高管理部门的承诺和参与。管理部门的承诺和参与,必须适时地、持续地表现出来,以确保在“改善”的过程中获得成功。
一,现场改善考虑下手的几个方面:
1、工艺流程查一查
即向工艺流程要效益。分析现有生产、工作的全过程,哪些工艺流程不合理,哪些地方出现了倒流,哪些地方出现了停放,包括储藏保管、停放状态、保管手段(如储存容器配备、货架配备、设施条件)、有无积压状态?哪些工艺路线和环节可以取消、合并、简化?寻找最佳停放条件,确定经济合理的工艺路线。
2、平面图上找一找
即向平面布置要效益。仔细检查和分析工厂平面布置图、车间平面布置图和设备平面布置图,分析作业方式和设备、设施的配置,按生产流程的流动方向,有无重复路线和倒流情况,找出不合理的部分,调整和设计一种新的布局,使生产流程在新的布置图上路线最短,配置最合理。
3、流水线上算一算
即向流水线要效益。研究流水线的节拍、每个工序的作业时间是否平衡,如果发现不平衡,就要通过裁并、简化、分解等等手法,平衡流水线。消除因个别工序缓慢而导致的窝工和堆积。
4、动作分析测一测
即向动作分析要效益。研究工作者的动作,分析人与物的结合状态,消除多余的动作、无效动作或缓慢动作,如弯腰作业、站在凳子上作业、蹲着作业、作业场所不畅、没有适合的工位器具、人与物处于寻找状态等,通过对人的动作和环境状态的分析和测定,确定合理的操作或工作方法;探讨减少人的无效劳动,消除浪费,解决现场杂乱,实现人和物紧密结合,提高作业效率。
5、搬运时空压一压
即向搬运时间和空间要效益。据统计,在产品生产中搬运和停顿时间约占70-80%,搬运的费用约占加工费的25-40%,要通过对搬运次数、搬运方法、搬运手段、搬运条件、搬运时间和搬运距离等综合分析,尽量减少搬运时间和空间,寻找最佳方法、手段和条件。
6、人机工程挤一挤
即向人机联合作业要效益。人和设备构成了人机工程,在分析时要分析作业者和机器在同一时间内的工作情况,有无窝工、等待、无效时间,通过调整工作顺序改进人机配合,寻求合理的方法,使人的操作和机器的运转协调配合,将等待时间减少到最大限度,充分发挥人和机器的效率。
7、关键路线缩一缩
即向网络技术要效益。将现有的工序和作业流程绘制成网络图。从中找出关键路线,然后从非关键路线上抽调人财物,加强关键路线,或采用平行作业。交差作业等等形式,实现时间和费用的优化。
8、场所环境变一变
分析生产、工作环境是否满足生产、工作需要和人的生理需要,分析5S现场管理还缺少什么物品和媒介物,针对不同类别场所的问题,分别提出改进建议,开展“整理、整顿、清扫、清洁、素养、安全”六项活动,做到永远保持A状态,不断改善B状态,随时清除C状态,使员工保持旺盛的斗志和良好的技能,所需物品随手可取,不需要之物随时得到清除,现场环境通畅、整洁、美化、安全、文明,使场所和环境在时间和空间上实现整体优化。
二,现场开展改善活动的过程中,要注意的问题:
1,工作量降低了但质量却恶化了。
2,虽然降低了0.7个人的工作量,但人却没减少。而周围的操作人有富余时间,在不断地摧促上一道工序的操作者加快速度。
3,作业虽然已小批量化,但步骤时间及库存量都却增加了。
4,达到了谋求少人化的目的,但设备投资却花了很多钱。
5,虽然已有所改善,但如果换了人又恢复了原状。
三,改善活动中的心态
1.好就是不好,不好就是好,要永无止境的改善下去.
好就是不好指的是失去了改善的机会,不好就是好指的是找到了改善的机会.把5S管理发挥到极致。
2.永无止境就是要追求:
(1)提高生产劳动率.
(2)减少不良率.
(3)缩短交期时间.
(4)降低库存,最好无库存.
(5)节省生产空间.
(6)提高设备可利用率.
3.就是有问题才去改善,不是没有问题就不去改善.
4.要打破传统一个人固定操作一个工位的思想,朝一个人多工序操作,弹性化方向发展.
5.掌握现场,现物,现实,现做,现查五现原则,不要只看书面的记录.
6.有50%的把握就要尝试去做,不要等到有100%的把握才去做改善.
7.改善要经历多次尝试才能成功,不是一次就能够全部成功.
8.要贯彻DIY的思想,马上动手做,不要在会议室里思考讨论.
9.用头脑智慧去克服问题,不是用金钱去摆平问题,不过可以通过用小钱去做大的事情.
10.要朝"理想状态"迈进,不要寻找不能做的原因,比如五没抵抗:没人,没钱,没时间,没空间,没条件.
11."理想状态"就是:
(1)依据产距时间生产.
(2)一个流方式生产.
(3)后拉式看板生产.
12.要发挥部门团队精神,共同努力达成目标.
13.要问五次为什么,找出问题的真正根源所在.
14.要顾全大局,例外情况特殊处理.
15.要观察有无三无现象并进行改善.
16.改善固然可喜,但是维持更是重要.
17.维持就是遵守标准作业,管理者要去督促检查是否有按标准作业.
18.要具备改善循环(PDCA)的四大意识,即品质意识、维持意识、问题意识、改善意识。
19.医生开处方,病人要吃药,老师教学生,学生要维持,指的是要把改善真正去实施起来。
20.问题就是机会,改善就是赚钱。
四,产生创意的思考法则:
1)相反法则-现行的方式逆向倒过来做,将会变得如何呢?
2)拼图法则-将每一基本部分分解出来,再尝试其它组合的方式,是否会有意想不到的效果呢?
3)大小法则-改变尺寸﹑形状等的大小,看看其影响会变得如何呢?
4)例外法则-将经常发生的事物与偶然发生的事物做区别,将偶然发生的状况加以例外管理原则来控制即可,而不要将经常发生的事物也用相同的管理方式来管理。
5)集合法则-尝试将不同的单元事物结合在一起,是否要以增加使用者的功用及效果?
6)更换法则-将顺序加以更换,效果是否会较好呢?
7)替代法则-考虑用别的方式来替代现有的方式,会有什么样的结果呢?
8)模仿法则-模仿是创造的最佳触媒,藉著参考现有的东西加以思考很容易引发新的创意出来。
9)水平法则-发挥自己的联想力,考虑由水平的方向去思考,突破传统及习惯上的束缚。
10)定数法则-将经常发生的事物予以制度化,可以产生许多简化的效果及提高效率。
免责声明:本文系转载,版权归原作者所有。新益为|精益管理视野鼓励原创行为,本文因转载众多无法找到原作者。如涉及版权,请联系电话023-67015863进行删除!
改进可再区分为“改善”(Kaizen)和“创新”(Innovation)。所谓“改善”,是由于持续不断的努力,所产生的诸多的小步伐改进,而逐次累积而成。“创新”则是借助大笔资源投资于新技术或设备,而产生戏剧性的变化的改进(不论任何场合,以金钱作为主要的评估因素时,创新便是昂贵的)。由于欧美的管理人员执迷于“创新”,他们既没有耐心,也忽视了“改善”能长期带给公司的利益。相反,“改善”则是强调要以员工的努力、士气、沟通、训练、团队、参与及5S培训自律来达成目标。这些都是一种常识性和低成本的改进方式。
“改善”是着重在“过程为导向”的思考模式上,这是因为要改进“结果”,必须先改进“过程”。预期的计划成果未能达成,表示其“过程”是失败的。管理部门必须确认及改正这种“过程面”的错误。“改善”是着重在“人际面”上的努力,此种东方的改善形态,恰与西方的着重在“结果面”的思想,形成尖锐的对比。以“过程为导向”的思想方式,应当运用在各种不同的改善活动上,诸如:计划→执行→核查→处置(PDCA)的循环、标准化→执行→核查→处置(SDCA)的循环、质量→成本→交期(QCD)的活动、全面质量管理(TQM)及时生产方式(JIT)和全员生产保全(TPM)。许多公司改善活动失败的原因,就在于轻忽“过程”。在“改善”的过程中,最关键性的就是最高管理部门的承诺和参与。管理部门的承诺和参与,必须适时地、持续地表现出来,以确保在“改善”的过程中获得成功。
一,现场改善考虑下手的几个方面:
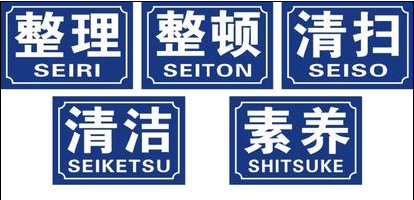
即向工艺流程要效益。分析现有生产、工作的全过程,哪些工艺流程不合理,哪些地方出现了倒流,哪些地方出现了停放,包括储藏保管、停放状态、保管手段(如储存容器配备、货架配备、设施条件)、有无积压状态?哪些工艺路线和环节可以取消、合并、简化?寻找最佳停放条件,确定经济合理的工艺路线。
2、平面图上找一找
即向平面布置要效益。仔细检查和分析工厂平面布置图、车间平面布置图和设备平面布置图,分析作业方式和设备、设施的配置,按生产流程的流动方向,有无重复路线和倒流情况,找出不合理的部分,调整和设计一种新的布局,使生产流程在新的布置图上路线最短,配置最合理。
3、流水线上算一算
即向流水线要效益。研究流水线的节拍、每个工序的作业时间是否平衡,如果发现不平衡,就要通过裁并、简化、分解等等手法,平衡流水线。消除因个别工序缓慢而导致的窝工和堆积。
4、动作分析测一测
即向动作分析要效益。研究工作者的动作,分析人与物的结合状态,消除多余的动作、无效动作或缓慢动作,如弯腰作业、站在凳子上作业、蹲着作业、作业场所不畅、没有适合的工位器具、人与物处于寻找状态等,通过对人的动作和环境状态的分析和测定,确定合理的操作或工作方法;探讨减少人的无效劳动,消除浪费,解决现场杂乱,实现人和物紧密结合,提高作业效率。
5、搬运时空压一压
即向搬运时间和空间要效益。据统计,在产品生产中搬运和停顿时间约占70-80%,搬运的费用约占加工费的25-40%,要通过对搬运次数、搬运方法、搬运手段、搬运条件、搬运时间和搬运距离等综合分析,尽量减少搬运时间和空间,寻找最佳方法、手段和条件。
6、人机工程挤一挤
即向人机联合作业要效益。人和设备构成了人机工程,在分析时要分析作业者和机器在同一时间内的工作情况,有无窝工、等待、无效时间,通过调整工作顺序改进人机配合,寻求合理的方法,使人的操作和机器的运转协调配合,将等待时间减少到最大限度,充分发挥人和机器的效率。
7、关键路线缩一缩
即向网络技术要效益。将现有的工序和作业流程绘制成网络图。从中找出关键路线,然后从非关键路线上抽调人财物,加强关键路线,或采用平行作业。交差作业等等形式,实现时间和费用的优化。
8、场所环境变一变
分析生产、工作环境是否满足生产、工作需要和人的生理需要,分析5S现场管理还缺少什么物品和媒介物,针对不同类别场所的问题,分别提出改进建议,开展“整理、整顿、清扫、清洁、素养、安全”六项活动,做到永远保持A状态,不断改善B状态,随时清除C状态,使员工保持旺盛的斗志和良好的技能,所需物品随手可取,不需要之物随时得到清除,现场环境通畅、整洁、美化、安全、文明,使场所和环境在时间和空间上实现整体优化。
二,现场开展改善活动的过程中,要注意的问题:
1,工作量降低了但质量却恶化了。
2,虽然降低了0.7个人的工作量,但人却没减少。而周围的操作人有富余时间,在不断地摧促上一道工序的操作者加快速度。
3,作业虽然已小批量化,但步骤时间及库存量都却增加了。
4,达到了谋求少人化的目的,但设备投资却花了很多钱。
5,虽然已有所改善,但如果换了人又恢复了原状。
三,改善活动中的心态
1.好就是不好,不好就是好,要永无止境的改善下去.
好就是不好指的是失去了改善的机会,不好就是好指的是找到了改善的机会.把5S管理发挥到极致。
2.永无止境就是要追求:
(1)提高生产劳动率.
(2)减少不良率.
(3)缩短交期时间.
(4)降低库存,最好无库存.
(5)节省生产空间.
(6)提高设备可利用率.
3.就是有问题才去改善,不是没有问题就不去改善.
4.要打破传统一个人固定操作一个工位的思想,朝一个人多工序操作,弹性化方向发展.
5.掌握现场,现物,现实,现做,现查五现原则,不要只看书面的记录.
6.有50%的把握就要尝试去做,不要等到有100%的把握才去做改善.
7.改善要经历多次尝试才能成功,不是一次就能够全部成功.
8.要贯彻DIY的思想,马上动手做,不要在会议室里思考讨论.
9.用头脑智慧去克服问题,不是用金钱去摆平问题,不过可以通过用小钱去做大的事情.
10.要朝"理想状态"迈进,不要寻找不能做的原因,比如五没抵抗:没人,没钱,没时间,没空间,没条件.
11."理想状态"就是:
(1)依据产距时间生产.
(2)一个流方式生产.
(3)后拉式看板生产.
12.要发挥部门团队精神,共同努力达成目标.
13.要问五次为什么,找出问题的真正根源所在.
14.要顾全大局,例外情况特殊处理.
15.要观察有无三无现象并进行改善.
16.改善固然可喜,但是维持更是重要.
17.维持就是遵守标准作业,管理者要去督促检查是否有按标准作业.
18.要具备改善循环(PDCA)的四大意识,即品质意识、维持意识、问题意识、改善意识。
19.医生开处方,病人要吃药,老师教学生,学生要维持,指的是要把改善真正去实施起来。
20.问题就是机会,改善就是赚钱。
四,产生创意的思考法则:
1)相反法则-现行的方式逆向倒过来做,将会变得如何呢?
2)拼图法则-将每一基本部分分解出来,再尝试其它组合的方式,是否会有意想不到的效果呢?
3)大小法则-改变尺寸﹑形状等的大小,看看其影响会变得如何呢?
4)例外法则-将经常发生的事物与偶然发生的事物做区别,将偶然发生的状况加以例外管理原则来控制即可,而不要将经常发生的事物也用相同的管理方式来管理。
5)集合法则-尝试将不同的单元事物结合在一起,是否要以增加使用者的功用及效果?
6)更换法则-将顺序加以更换,效果是否会较好呢?
7)替代法则-考虑用别的方式来替代现有的方式,会有什么样的结果呢?
8)模仿法则-模仿是创造的最佳触媒,藉著参考现有的东西加以思考很容易引发新的创意出来。
9)水平法则-发挥自己的联想力,考虑由水平的方向去思考,突破传统及习惯上的束缚。
10)定数法则-将经常发生的事物予以制度化,可以产生许多简化的效果及提高效率。
免责声明:本文系转载,版权归原作者所有。新益为|精益管理视野鼓励原创行为,本文因转载众多无法找到原作者。如涉及版权,请联系电话023-67015863进行删除!