分析何为企业的TPM管理活动
来源/作者:未知 发布时间:2013年12月19日 阅读次数:次
TPM管理活动在企业中推行是企业的一项重大活动,TPM的全员性即在开展TPM管理活动的过程中,企业的全体人员都要参加到活动中来。任何人都可以参加到企业设备维护的简单工作中来。
TPM起源于“全员质量管理(TQM)”。TQM是W•爱德华•德明博士对日本工业产生影响的直接结果。德明博士在二战后不久就到日本开展他的工作。作为一名统计学家,他最初只是负责教授日本人如何在其制造业中运用统计分析。进而如何利用其数据结果,在制造过程中控制产品质量。最初的统计过程及其产生的质量控制原理不久受到日本人职业道德的影响,形成了具有日本特色的工业生存之道,这种新型的制造概念最终形成了众所周知TQM。
当TQM要求将设备维修作为其中一项检验要素时,发现TQM本身似乎并不适合维修环境。这是由于在相当一段时间内,人们重视的是预防性维修(PM)措施,多数工厂也都采用PM,而且,通过采用PM技术制定维修计划以保持设备正常运转的技术业已成熟。然而在需要提高或改进产量时,这种技术时常导致对设备的过度保养。它的指导思想是:“如果有一滴油能好一点,那么有较多的油应该会更好”。这样一来,要提高设备运转速度必然会导致维修作业的增加。
而在通常的维修过程中,很少或根本就不考虑操作人员的作用,维修人员也只是就常用的并不完善的维修手册规定的内容进行培训,并不涉及额外的知识。
通过采用TPM,许多公司很快意识到要想仅仅通过对维修进行规划来满足制造需求是远远不够的。要在遵循TQM原则前提下解决这一问题,需要对最初的TPM技术进行改进,以便将维修纳入到整个质量过程的组成部分之中。
TPM的出处已经明确。TPM最早是在40年前由一位美国制造人员提出的。但最早将TPM技术引入维修领域的是日本的一位汽车电子元件制造商——Nippondenso在20世纪60年代后期实现的。后来,日本工业维修协会干事SeiichiNakajima对TPM作了界定并目睹了TPM在数百家日本公司中的应用。
从理论上讲,TPM是一种维修程序。它与TQM(全员质量管理)有以下几点相似之处:(1)要求将包括高级管理层在内的公司全体人员纳入TPM;
(2)要求必须授权公司员工可以按TPM分工协议自主按标准进行校正作业;
(3)要求有一个较长的作业期限,这是因为TPM自身有一个发展过程,贯彻TPM需要约一年甚至更多的时间,而且使公司员工从思想上转变也需要时间。
TPM将维修变成了企业中必不可少的和极其重要的组成部分,维修停机时间也成了工作日计划表中不可缺少的一项,而维修也不再是一项没有效益的作业。在某些情况下可将维修视为整个制造过程的组成部分,而不是简单地在流水线出现故障后进行,其目的是将应急的和计划外的维修最小化。
TPM管理活动在企业中开展,如果企业想要使得TPM管理活动的效果再进一步,可以在企业中开展5S管理活动,5S管理是企业管理的基础,所以开展好企业的5S管理,能让企业的TPM管理活动更进一步。
免责声明:本文系转载,版权归原作者所有。新益为|精益管理视野鼓励原创行为,本文因转载众多无法找到原作者。如涉及版权,请联系电话023-67015863进行删除!
TPM起源于“全员质量管理(TQM)”。TQM是W•爱德华•德明博士对日本工业产生影响的直接结果。德明博士在二战后不久就到日本开展他的工作。作为一名统计学家,他最初只是负责教授日本人如何在其制造业中运用统计分析。进而如何利用其数据结果,在制造过程中控制产品质量。最初的统计过程及其产生的质量控制原理不久受到日本人职业道德的影响,形成了具有日本特色的工业生存之道,这种新型的制造概念最终形成了众所周知TQM。
当TQM要求将设备维修作为其中一项检验要素时,发现TQM本身似乎并不适合维修环境。这是由于在相当一段时间内,人们重视的是预防性维修(PM)措施,多数工厂也都采用PM,而且,通过采用PM技术制定维修计划以保持设备正常运转的技术业已成熟。然而在需要提高或改进产量时,这种技术时常导致对设备的过度保养。它的指导思想是:“如果有一滴油能好一点,那么有较多的油应该会更好”。这样一来,要提高设备运转速度必然会导致维修作业的增加。
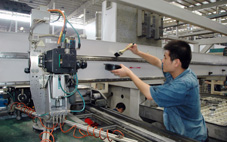
通过采用TPM,许多公司很快意识到要想仅仅通过对维修进行规划来满足制造需求是远远不够的。要在遵循TQM原则前提下解决这一问题,需要对最初的TPM技术进行改进,以便将维修纳入到整个质量过程的组成部分之中。
TPM的出处已经明确。TPM最早是在40年前由一位美国制造人员提出的。但最早将TPM技术引入维修领域的是日本的一位汽车电子元件制造商——Nippondenso在20世纪60年代后期实现的。后来,日本工业维修协会干事SeiichiNakajima对TPM作了界定并目睹了TPM在数百家日本公司中的应用。
从理论上讲,TPM是一种维修程序。它与TQM(全员质量管理)有以下几点相似之处:(1)要求将包括高级管理层在内的公司全体人员纳入TPM;
(2)要求必须授权公司员工可以按TPM分工协议自主按标准进行校正作业;
(3)要求有一个较长的作业期限,这是因为TPM自身有一个发展过程,贯彻TPM需要约一年甚至更多的时间,而且使公司员工从思想上转变也需要时间。
TPM将维修变成了企业中必不可少的和极其重要的组成部分,维修停机时间也成了工作日计划表中不可缺少的一项,而维修也不再是一项没有效益的作业。在某些情况下可将维修视为整个制造过程的组成部分,而不是简单地在流水线出现故障后进行,其目的是将应急的和计划外的维修最小化。
TPM管理活动在企业中开展,如果企业想要使得TPM管理活动的效果再进一步,可以在企业中开展5S管理活动,5S管理是企业管理的基础,所以开展好企业的5S管理,能让企业的TPM管理活动更进一步。
免责声明:本文系转载,版权归原作者所有。新益为|精益管理视野鼓励原创行为,本文因转载众多无法找到原作者。如涉及版权,请联系电话023-67015863进行删除!