精益生产流程管理——价值流应用步骤
来源/作者:未知 发布时间:2014年12月25日 阅读次数:次
精益生产流程管理的目的是消除流程中不增值的活动,使流程价值最大化。为了更好分析与改善流程的价值增值书评,一种的新的流程分析工具---价值流程,可以帮助企业进行流程精益生产进行改造。
价值流,能够帮助价值流改进小组成员纵观全局来分析目前状态:该步骤为顾客创造价值了吗?该步骤充分发挥作用了吗?该步骤适用吗?该步骤是柔性的吗?该步骤的产能充足吗?产品流程无须等待吗?或者该步骤产能过大吗?
价值流图应用步骤如下:
1、选择一个价值流(产品族)
首先选择一个价值流(产品族),这种产品(或者产品系列)应该是企业最重要的产品,或是价值流现状不好,需要改善的产品。
2、描绘目前状态。
确定了进行价值流分析的产品或产品系列以后,就要描述该产品的价值流图现状。主要步骤如下:
①获取顾客需求数据。开始做任何改善时,最重要的是从最终顾客的角度确认产品的价值,否则,即便改善了价值流,也无法最终满足顾客真正的需求。所以,绘图从顾客要求开始,先了解客户需求。
②收集各工序的实际数据及现场在制品库存数据。为了绘制价值流图,需要收集有关流程的数据。数据主要有:C/T(周期时间);C/O(换模时间);操作工数量、工作班次、废品率等。当发现有库存堆积的地方时,要标示库存数量,并记录库存的地点。
由于价值流描绘强调的是现场数据,所以在采集数据的时候,应尽量以现场5S管理实际情况为准,保证数据真实反映现场操作状态;部分数据如切换时间、废品率等,可以取用历史数据,取用的历史数据,必须是最近的,不能用太长时间以前的数据。
③在图中标识成品及原材料的流动。在图的另一端,用另一个工厂图标代表原材料供应商。用货车和粗箭头,表示原材料运输。
死描绘整个产品实现过程中的信息流。价值流图中的每一个过程用一个框表示,框内显示一些时间、资源、工作班次等信息。两个过程之间如果有库存,则显示库存存放时间长短。
3、当前状态价值流分析
从现状价值流图可以很容易地对生产体系的现状进行分析,找出有利于增值的最佳方式,然后对生产体系进行改进,从而设计出目标价值流图。
4、未来价值流描绘
通过对现状价值流的分析,找出有关改善价值流的问题,提出有关措施以后,可以建立一个新的未来价值流图。
5、价值流改进计划。
根据现状图和未来图,可以找出改进的机会。根据改进的机会图,可以制订详细的计划,精益生产以实现价值流未来图。要实现未来图,采用拉动生产方式、生产线平衡方法和技术。
免责声明:本文系转载,版权归原作者所有。新益为|精益管理视野鼓励原创行为,本文因转载众多无法找到原作者。如涉及版权,请联系电话023-67015863进行删除!
价值流,能够帮助价值流改进小组成员纵观全局来分析目前状态:该步骤为顾客创造价值了吗?该步骤充分发挥作用了吗?该步骤适用吗?该步骤是柔性的吗?该步骤的产能充足吗?产品流程无须等待吗?或者该步骤产能过大吗?
价值流图应用步骤如下:
1、选择一个价值流(产品族)
首先选择一个价值流(产品族),这种产品(或者产品系列)应该是企业最重要的产品,或是价值流现状不好,需要改善的产品。
2、描绘目前状态。
确定了进行价值流分析的产品或产品系列以后,就要描述该产品的价值流图现状。主要步骤如下:
①获取顾客需求数据。开始做任何改善时,最重要的是从最终顾客的角度确认产品的价值,否则,即便改善了价值流,也无法最终满足顾客真正的需求。所以,绘图从顾客要求开始,先了解客户需求。
②收集各工序的实际数据及现场在制品库存数据。为了绘制价值流图,需要收集有关流程的数据。数据主要有:C/T(周期时间);C/O(换模时间);操作工数量、工作班次、废品率等。当发现有库存堆积的地方时,要标示库存数量,并记录库存的地点。
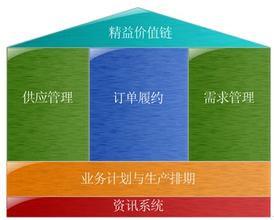
由于价值流描绘强调的是现场数据,所以在采集数据的时候,应尽量以现场5S管理实际情况为准,保证数据真实反映现场操作状态;部分数据如切换时间、废品率等,可以取用历史数据,取用的历史数据,必须是最近的,不能用太长时间以前的数据。
③在图中标识成品及原材料的流动。在图的另一端,用另一个工厂图标代表原材料供应商。用货车和粗箭头,表示原材料运输。
死描绘整个产品实现过程中的信息流。价值流图中的每一个过程用一个框表示,框内显示一些时间、资源、工作班次等信息。两个过程之间如果有库存,则显示库存存放时间长短。
3、当前状态价值流分析
从现状价值流图可以很容易地对生产体系的现状进行分析,找出有利于增值的最佳方式,然后对生产体系进行改进,从而设计出目标价值流图。
4、未来价值流描绘
通过对现状价值流的分析,找出有关改善价值流的问题,提出有关措施以后,可以建立一个新的未来价值流图。
5、价值流改进计划。
根据现状图和未来图,可以找出改进的机会。根据改进的机会图,可以制订详细的计划,精益生产以实现价值流未来图。要实现未来图,采用拉动生产方式、生产线平衡方法和技术。
免责声明:本文系转载,版权归原作者所有。新益为|精益管理视野鼓励原创行为,本文因转载众多无法找到原作者。如涉及版权,请联系电话023-67015863进行删除!