浅谈精益生产管理的实施策略与方法
来源/作者:未知 发布时间:2014年10月11日 阅读次数:次
实施精益生产讲究方法和运用策略,企业在实行精益生产的过程中,培养依靠员工、发现问题、持续改进的企业文化是非常关键的。
(1)准时制生产的导入
JIT生产方式是一种生产管理理念,精益生产是对JIT生产方式的进一步提炼和总结。精益生产的实施是建立在一系列生产管理技术之上的,如看板管理、均衡化生产、全面质量管理、准时采购等。这些精益工具非常适合将问题暴露出来,促使员工不断成长,支持持续改善文化的建立。下图介绍了准时制生产方式导入的一般步骤。
需要注意的是,企业必须在推行JIT的基础上去使用MRP。
(2)工业工程方法
工业工程(IndustrialEngineering,IE)形成于19世纪末20世纪初的美国人泰勒等发起的科学管理运动,是改善效率、成本、质量的一门方法学,就是把技术和管理有机地结合起来,研究如何使生产要素组成更高效运行的系统,从而实现提高生产率的目标。美国工业工程学会(AmericanInstituteofIndustrialEngineering,AIIE)对工业工程的定义是:研究由人、物料、信息、设备和能源构成的集成系统的设计、改进和实施,它应用数学、物理学和社会科学的知识和技能,结合工程分析和设计的原理与方法,来说明、预测和评价这一集成系统将得到的结果。
丰田生产方式就是工业工程在丰田公司现代管理中的应用。可以说工业工程是丰田生产方式实现的支撑性技术体系,特别是改善活动依托的原理与方法主要是IE。工业工程既是完成精益生产方式的工程与管理基础,又是精益生产的重要组成部分。
IE推行简单化、专门化和标准化,通过改进方法和程序,以求降低成本,提高质量和劳动生产率,追求生产系统的最佳整体效益。日本企业在推行精益生产时,运用基础IE中大量的作业研究、动作研究、时间分析技术,调查机械的能力,编制标准作业表,使精益生产不仅带来了生产组织方式的质变,而且带来了产品开发、质量控制、内外协作管理、与用户关系等一连串根本性的企业组织体制、管理体制方面的重大变化。IE方法贯穿精益生产的整个过程中,从工作研究、作业分析、动作和微动作分析到研究制定作业标准,从各种现场管理优化到各类产品生产过程及服务过程中的增值问题等都需要IE发挥作用。企业在实施精益生产中要从推行IE入手,运用IE方法持续进行改善。
(3)推行5S管理
5S是指整理(Seiri),整顿(Seiton)、清扫(Seiso)、清洁(Seiketsu)和素养(Shitsuke)五个项目,因日语的拼音均以“S”开头,简称5S。整理是区分要与不要,将不需要的东西及时清理出现场;整顿是对整理后需要的物品进行合理摆放;清扫是清除垃圾、油水、杂物、铁屑等;清洁是维持整理、整顿、清扫的状态,使设备、工艺装备、工位器具、零件无污物,环境清洁美化;素养是通过前“4S",使人们的道德观念和纪律得到加强,做到严格遵守规章制度,尊重他人劳动,养成良好的习惯。5S强调从小事做起,要求全员参与。通过一系列手段塑造一个干净、整洁、一目了然的工作环境,最终提升人的素养:有规定按规定去做。
5S是现场管理的基础管理技术,是实现精益生产方式的基础。在一个没有实施5S的企业,员工没有养成“有规定按规定去做”的职业素养,浪费现象随处可见。精益生产的本质是要消除浪费,在一个没有5S基础的企业中实施精益生产是很难取得好效果的。不推行5S管理,难以实现精益生产。
在企业成功推行5S的主要步骤为:5S推行组织的建立;制订5s活动计划,包括整体规划、教育训练、活动方案及日程设计,责任区域的划分及负责人确定,制定实施方法,制定评鉴方法,制定奖惩方法;5S活动的宣导、教育训练;整理、整顿;应用看板管理及目视管理;考核评分;改善实施;上级巡回诊断;检讨与奖惩;制度标准化,通过PDCA循环将推行过程中的成功方法和良好经验加以标准化、制度化,为企业持续改进打下基础。
(5)打造精益供应链
精益供应链就是将从产品设计到顾客得到产品的整个过程所必需的步骤和合作伙伴整合起来,快速响应顾客多变的需求,其核心就是用尽可能少的资源最大限度地满足客户需求。这一思想源于准时制生产精益思想和TOC理论。精益思想的核心是消除流程中的各种浪费,包括库存、运输距离、等待时间等,企业组织得以精简,流程得以优化,从而压缩了提前期,提高了对市场的响应速度。约束理论强调系统思维,合理利用企业有限的资源创造最大的价值流。
多变的顾客需求和市场环境要求加强企业间的协作与信息共享,消除牛鞭效应带来的负面影响。可以从下面几个方面打造精益供应链的策略:
①产品和流程模块化。将最终产品分解成可被单独制造和存储的模块,不同产品可以用相同的流程来制造。模块化有利于并行工程的实施,提高响应速度。
②延迟差异化策略.将同类产品中有差异部分的生产尽量推迟,以获得更多有关差异部分的信息。
③用能力而不是库存。库存是浪费,能力可以转化成库存,因此应该通过能力来应对需求不确定性。通过保持一定的冗余产能来应对紧急订单的生产。
④通过协调外部资源来扩充能力。
⑤建立柔性的生产能力。
打造精益供应链包括两个步骤:第一步是绘制企业目前供应链的价值流图;第二步是绘制一个供应链的理想价值流图。过程中应遵循减少浪费、可视化管理、减少库存、实现均衡拉动、缩短交付时间等精益原则。
(6)尊重员工
尊重员工是日本企业实现改进的关键原因,这与日本强调终身雇佣的传统也有一定关系。管理者们把员工看成是财富,给每个员工提供能充分展示他们能力的机会。员工采取更加积极主动的态度来帮助公司完成其目标。丰田生产方式被称为“尊重人性”的制度,包括一套专门设计以促成员工持续改善与发展的工具。在员工教育方面,丰田训练杰出的个人和团队以实现公司理念,运用跨部门团队以提高品质与生产效率,解决困难的技术问题,以改进流程。在作业改善中尊重人格,鼓励员工提建议,把员工的能力与有意义的有效作业结合起来,同时又能激发员工的热情、干劲和智慧,提高工作效率。让员工明白企业的未来就是自已的未来。推行精益生产是条任重而道远的路。
免责声明:本文系转载,版权归原作者所有。新益为|精益管理视野鼓励原创行为,本文因转载众多无法找到原作者。如涉及版权,请联系电话023-67015863进行删除!
(1)准时制生产的导入
JIT生产方式是一种生产管理理念,精益生产是对JIT生产方式的进一步提炼和总结。精益生产的实施是建立在一系列生产管理技术之上的,如看板管理、均衡化生产、全面质量管理、准时采购等。这些精益工具非常适合将问题暴露出来,促使员工不断成长,支持持续改善文化的建立。下图介绍了准时制生产方式导入的一般步骤。
需要注意的是,企业必须在推行JIT的基础上去使用MRP。
(2)工业工程方法
工业工程(IndustrialEngineering,IE)形成于19世纪末20世纪初的美国人泰勒等发起的科学管理运动,是改善效率、成本、质量的一门方法学,就是把技术和管理有机地结合起来,研究如何使生产要素组成更高效运行的系统,从而实现提高生产率的目标。美国工业工程学会(AmericanInstituteofIndustrialEngineering,AIIE)对工业工程的定义是:研究由人、物料、信息、设备和能源构成的集成系统的设计、改进和实施,它应用数学、物理学和社会科学的知识和技能,结合工程分析和设计的原理与方法,来说明、预测和评价这一集成系统将得到的结果。
丰田生产方式就是工业工程在丰田公司现代管理中的应用。可以说工业工程是丰田生产方式实现的支撑性技术体系,特别是改善活动依托的原理与方法主要是IE。工业工程既是完成精益生产方式的工程与管理基础,又是精益生产的重要组成部分。
IE推行简单化、专门化和标准化,通过改进方法和程序,以求降低成本,提高质量和劳动生产率,追求生产系统的最佳整体效益。日本企业在推行精益生产时,运用基础IE中大量的作业研究、动作研究、时间分析技术,调查机械的能力,编制标准作业表,使精益生产不仅带来了生产组织方式的质变,而且带来了产品开发、质量控制、内外协作管理、与用户关系等一连串根本性的企业组织体制、管理体制方面的重大变化。IE方法贯穿精益生产的整个过程中,从工作研究、作业分析、动作和微动作分析到研究制定作业标准,从各种现场管理优化到各类产品生产过程及服务过程中的增值问题等都需要IE发挥作用。企业在实施精益生产中要从推行IE入手,运用IE方法持续进行改善。
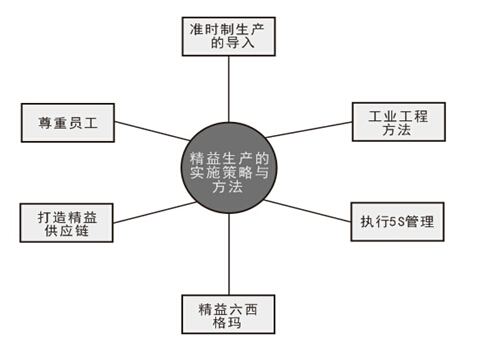
5S是指整理(Seiri),整顿(Seiton)、清扫(Seiso)、清洁(Seiketsu)和素养(Shitsuke)五个项目,因日语的拼音均以“S”开头,简称5S。整理是区分要与不要,将不需要的东西及时清理出现场;整顿是对整理后需要的物品进行合理摆放;清扫是清除垃圾、油水、杂物、铁屑等;清洁是维持整理、整顿、清扫的状态,使设备、工艺装备、工位器具、零件无污物,环境清洁美化;素养是通过前“4S",使人们的道德观念和纪律得到加强,做到严格遵守规章制度,尊重他人劳动,养成良好的习惯。5S强调从小事做起,要求全员参与。通过一系列手段塑造一个干净、整洁、一目了然的工作环境,最终提升人的素养:有规定按规定去做。
5S是现场管理的基础管理技术,是实现精益生产方式的基础。在一个没有实施5S的企业,员工没有养成“有规定按规定去做”的职业素养,浪费现象随处可见。精益生产的本质是要消除浪费,在一个没有5S基础的企业中实施精益生产是很难取得好效果的。不推行5S管理,难以实现精益生产。
在企业成功推行5S的主要步骤为:5S推行组织的建立;制订5s活动计划,包括整体规划、教育训练、活动方案及日程设计,责任区域的划分及负责人确定,制定实施方法,制定评鉴方法,制定奖惩方法;5S活动的宣导、教育训练;整理、整顿;应用看板管理及目视管理;考核评分;改善实施;上级巡回诊断;检讨与奖惩;制度标准化,通过PDCA循环将推行过程中的成功方法和良好经验加以标准化、制度化,为企业持续改进打下基础。
(5)打造精益供应链
精益供应链就是将从产品设计到顾客得到产品的整个过程所必需的步骤和合作伙伴整合起来,快速响应顾客多变的需求,其核心就是用尽可能少的资源最大限度地满足客户需求。这一思想源于准时制生产精益思想和TOC理论。精益思想的核心是消除流程中的各种浪费,包括库存、运输距离、等待时间等,企业组织得以精简,流程得以优化,从而压缩了提前期,提高了对市场的响应速度。约束理论强调系统思维,合理利用企业有限的资源创造最大的价值流。
多变的顾客需求和市场环境要求加强企业间的协作与信息共享,消除牛鞭效应带来的负面影响。可以从下面几个方面打造精益供应链的策略:
①产品和流程模块化。将最终产品分解成可被单独制造和存储的模块,不同产品可以用相同的流程来制造。模块化有利于并行工程的实施,提高响应速度。
②延迟差异化策略.将同类产品中有差异部分的生产尽量推迟,以获得更多有关差异部分的信息。
③用能力而不是库存。库存是浪费,能力可以转化成库存,因此应该通过能力来应对需求不确定性。通过保持一定的冗余产能来应对紧急订单的生产。
④通过协调外部资源来扩充能力。
⑤建立柔性的生产能力。
打造精益供应链包括两个步骤:第一步是绘制企业目前供应链的价值流图;第二步是绘制一个供应链的理想价值流图。过程中应遵循减少浪费、可视化管理、减少库存、实现均衡拉动、缩短交付时间等精益原则。
(6)尊重员工
尊重员工是日本企业实现改进的关键原因,这与日本强调终身雇佣的传统也有一定关系。管理者们把员工看成是财富,给每个员工提供能充分展示他们能力的机会。员工采取更加积极主动的态度来帮助公司完成其目标。丰田生产方式被称为“尊重人性”的制度,包括一套专门设计以促成员工持续改善与发展的工具。在员工教育方面,丰田训练杰出的个人和团队以实现公司理念,运用跨部门团队以提高品质与生产效率,解决困难的技术问题,以改进流程。在作业改善中尊重人格,鼓励员工提建议,把员工的能力与有意义的有效作业结合起来,同时又能激发员工的热情、干劲和智慧,提高工作效率。让员工明白企业的未来就是自已的未来。推行精益生产是条任重而道远的路。
免责声明:本文系转载,版权归原作者所有。新益为|精益管理视野鼓励原创行为,本文因转载众多无法找到原作者。如涉及版权,请联系电话023-67015863进行删除!