推行精益生产现场管理遇到的障碍与解决途径
来源/作者:未知 发布时间:2014年09月26日 阅读次数:次
精益生产管理推行在各个企业的管理者都在或多或少的进行,在精益推行的过程当中,不是一帆风顺的。大家都有这样的想法,也有推行精益的志愿,但是能否在企业当中顺利实施,这是每一个企业都面临的问题和困难。
在我咨询的很多企业当中,他们也存在很多的困惑和障碍,包括企业的管理者,也包括我自身。如何来认识这些障碍、冲破这些障碍,这是我们我多年来认真思考和总结交流的一部分,利用一个小时的时间和大家一起交流,冲破障碍、踏入坦途,看看如何让精益管理在我们的车间、在我们的工厂能够真的踏入坦途,真正落地。
在接下来的时段,分四个部门和大家进行交流。第一,推进精益现场面临的障碍到底是什么?第二,到底是什么原因使这些摘要产生,我们如何理解在现场产生的障碍的根源,就是如何正确的理解现场;第三,面对这些问题,克服这些障碍的行动和途径,到底员工和管理者应该如何在现场给员工作出回答,如何给心中的障碍作出回答;第四部分就是案例和交流。
精益的推行面临着障碍,绝大多数企业都是一样的。在一开始,我们信誓旦旦的推行精益生产,精益生产在很多的企业确实能够在初期很好的被应用,会有很好的效果。但是过一段时间以后,就会出现改善停留在表面,只是简单的现场变化,达不到预期的心理期望。不像丰田公司,他们为什么能够做得很好,而且能够长久的来维持呢?比如说今天好了,过一个月又反弹了。有很多的管理板目视管理很好,但是现场感觉是空的,没有实在的东西,得不到很好的管理应用,员工的参与度、热情逐渐降低,这些障碍和困惑产生的根源到底是什么呢?
员工素质低到底是不是这样一种障碍,丰田公司的员工好、素质高,很多的管理者在我咨询的过程当中都说他们公司的员工天高皇帝远,没有见过世面,没有丰田公司或者欧美企业员工的素质,有的员工都没有念过书,是不是我们的员工比丰田、比国外的员工就差呢?现在我们分析推行过程中的问题
第一点,基于长期的理念,即使牺牲短期的财务目标也在所不惜,我要达到我的管理方式,我要达到我的经营理念。在很多的时候,我们在想,来了一个紧急订单,生产现场发现异常,需要我们进行自动化,需要我们进行调整的时候,很多时候不管怎么样我只要结果,必须要完成。那么是不是遵循这种模式的基础呢?你敢不敢停下来,你敢不敢坚持你想要达成的目标?作为丰田模式支撑的两大模式,包括昨天完善,我们保持和尊重员工,在这个基础下又细分了五个方面,第一个激励机制,你有什么样的管理机制来支撑你的理念,这是不能变的,各种法律和条款我们都可以,基本不能动的,所以还要有一部分作为激励机制和管理机制。在流程中和跟事业伙伴合作中强调的是持续改善和合作,尊重员工、尊重领导,尊重我的供应商,大家一起共同的做一些事情,要持续的进行改善。
最后一点也是最关键的,就是现地现物的解决问题。丰田公司的现场和很多企业现场表面看来没有什么两样,实际上丰田公司每时每刻都在发生着改善和解决问题,这些是丰田模式的跟随也是他们的精髓,是很多没有学到,它不能理解,在这种模式的理解下,才真的把它变成了支撑精益生产方式的运行。要把这种模式变成每一个员工日常的交流和工作的取向,是每一个人都这样想,每一个部门都这样想,它才能支撑着精益生产方式准时化和自动化。没有这个模式的架构,没有这五个基础,你架构的只是工具、方法,它只能会反弹。
在这个模式下,我们强调的是全面系统的观点,精益生产管理是生产部门的事情,这是大错特错的,应该是全系统的观念。昨天大家就在想我的浪费有很多的浪费,让我的生产现场很苦恼、很困惑,所以它是全系统的观点。
第二就是要不断的进行培训,提升员工认识问题和解决问题的能力。就是叫精益工具为员工持续改善提供支持,要提高他的思维,要提升他的眼力,让他到现场以后就可以发现问题。
第三是以过程为导向,要管理过程。不是单纯的5S管理结果,很多的管理者就是这样,最后一个报表过来一看,觉得挺好或者不行,那就已经晚了。
第四就是员工要持续改善。作为精益生产,它的基础是什么?一定是系统架构和人才育成。现在对企业的评价就是我的固定资产是多少,我的产值是多少,那是虚的,最后要看你的员工能力和积极性。员工的积极性打一个折扣,整个企业的财富就打一个折扣,员工的能力打一个折扣,我企业的财富就打一个折扣。无论你有多少好的厂房、多少好的设备,所以要想架构精益生产方式,它的一切一定要打牢,它的模式我们一定要理解好,就是系统架构和人才育成。
免责声明:本文系转载,版权归原作者所有。新益为|精益管理视野鼓励原创行为,本文因转载众多无法找到原作者。如涉及版权,请联系电话023-67015863进行删除!
在我咨询的很多企业当中,他们也存在很多的困惑和障碍,包括企业的管理者,也包括我自身。如何来认识这些障碍、冲破这些障碍,这是我们我多年来认真思考和总结交流的一部分,利用一个小时的时间和大家一起交流,冲破障碍、踏入坦途,看看如何让精益管理在我们的车间、在我们的工厂能够真的踏入坦途,真正落地。
在接下来的时段,分四个部门和大家进行交流。第一,推进精益现场面临的障碍到底是什么?第二,到底是什么原因使这些摘要产生,我们如何理解在现场产生的障碍的根源,就是如何正确的理解现场;第三,面对这些问题,克服这些障碍的行动和途径,到底员工和管理者应该如何在现场给员工作出回答,如何给心中的障碍作出回答;第四部分就是案例和交流。
精益的推行面临着障碍,绝大多数企业都是一样的。在一开始,我们信誓旦旦的推行精益生产,精益生产在很多的企业确实能够在初期很好的被应用,会有很好的效果。但是过一段时间以后,就会出现改善停留在表面,只是简单的现场变化,达不到预期的心理期望。不像丰田公司,他们为什么能够做得很好,而且能够长久的来维持呢?比如说今天好了,过一个月又反弹了。有很多的管理板目视管理很好,但是现场感觉是空的,没有实在的东西,得不到很好的管理应用,员工的参与度、热情逐渐降低,这些障碍和困惑产生的根源到底是什么呢?
员工素质低到底是不是这样一种障碍,丰田公司的员工好、素质高,很多的管理者在我咨询的过程当中都说他们公司的员工天高皇帝远,没有见过世面,没有丰田公司或者欧美企业员工的素质,有的员工都没有念过书,是不是我们的员工比丰田、比国外的员工就差呢?现在我们分析推行过程中的问题
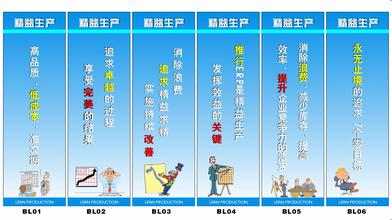
第一点,基于长期的理念,即使牺牲短期的财务目标也在所不惜,我要达到我的管理方式,我要达到我的经营理念。在很多的时候,我们在想,来了一个紧急订单,生产现场发现异常,需要我们进行自动化,需要我们进行调整的时候,很多时候不管怎么样我只要结果,必须要完成。那么是不是遵循这种模式的基础呢?你敢不敢停下来,你敢不敢坚持你想要达成的目标?作为丰田模式支撑的两大模式,包括昨天完善,我们保持和尊重员工,在这个基础下又细分了五个方面,第一个激励机制,你有什么样的管理机制来支撑你的理念,这是不能变的,各种法律和条款我们都可以,基本不能动的,所以还要有一部分作为激励机制和管理机制。在流程中和跟事业伙伴合作中强调的是持续改善和合作,尊重员工、尊重领导,尊重我的供应商,大家一起共同的做一些事情,要持续的进行改善。
最后一点也是最关键的,就是现地现物的解决问题。丰田公司的现场和很多企业现场表面看来没有什么两样,实际上丰田公司每时每刻都在发生着改善和解决问题,这些是丰田模式的跟随也是他们的精髓,是很多没有学到,它不能理解,在这种模式的理解下,才真的把它变成了支撑精益生产方式的运行。要把这种模式变成每一个员工日常的交流和工作的取向,是每一个人都这样想,每一个部门都这样想,它才能支撑着精益生产方式准时化和自动化。没有这个模式的架构,没有这五个基础,你架构的只是工具、方法,它只能会反弹。
在这个模式下,我们强调的是全面系统的观点,精益生产管理是生产部门的事情,这是大错特错的,应该是全系统的观念。昨天大家就在想我的浪费有很多的浪费,让我的生产现场很苦恼、很困惑,所以它是全系统的观点。
第二就是要不断的进行培训,提升员工认识问题和解决问题的能力。就是叫精益工具为员工持续改善提供支持,要提高他的思维,要提升他的眼力,让他到现场以后就可以发现问题。
第三是以过程为导向,要管理过程。不是单纯的5S管理结果,很多的管理者就是这样,最后一个报表过来一看,觉得挺好或者不行,那就已经晚了。
第四就是员工要持续改善。作为精益生产,它的基础是什么?一定是系统架构和人才育成。现在对企业的评价就是我的固定资产是多少,我的产值是多少,那是虚的,最后要看你的员工能力和积极性。员工的积极性打一个折扣,整个企业的财富就打一个折扣,员工的能力打一个折扣,我企业的财富就打一个折扣。无论你有多少好的厂房、多少好的设备,所以要想架构精益生产方式,它的一切一定要打牢,它的模式我们一定要理解好,就是系统架构和人才育成。
免责声明:本文系转载,版权归原作者所有。新益为|精益管理视野鼓励原创行为,本文因转载众多无法找到原作者。如涉及版权,请联系电话023-67015863进行删除!