避免认识误区需要如何正确理解精益生产
来源/作者:未知 发布时间:2014年09月02日 阅读次数:次
精益生产思想从一种自觉的尝试开始,通过与用户的对话,为具有特定功能以特定价格提供的产品精确定义价值。
问一、推动实施精益成功的企业并不多,如何才能提高成功率?
答:推行精益是个系统的工程,要成功地推行精益首先要从万里高空去俯瞰这个企业的问题。推行精益实际是个生产方式重新架构的问题,我们常说TPS是丰田生产方式或者丰田生产系统,就是把它看成一个系统的。所以一个企业要推行精益时首先要回答这个问题,你的生产系统需要什么样的变化才能让你这个企业在质量,成本,交期上有着质的提高。推行精益生产培训和咨询活动成功的标志也是是否让你这个企业成为同行“最佳公司”之一。
从多年推行精益的实践上来看,我认为推行精益的成功要素主要有三点。
精益的方法和工具
精益活动的管理
精益的领导力。
这三点是有层次关系的,从1到3是从下往上的关系。
精益的方法和工具。最常见的就是TPS屋,很多人就把它当成整个丰田生产方式的了,其实这是有误区的,它只解释了丰田生产方式技术上的架构,也可以之为硬件结构。推行精益成功的另两个更重要的要素:改善活动的管理和领导力却没提及。
精益活动的管理本身也包括三大块:1是推动精益的组织结构,2是精益活动的组织和管理,3是信息交流。第一块:改善的组织结构与相应的职能可参见下客户例:
第二块精益活动的组织和管理核心工作内容主要有以下几点:
员工精益知识和技能的培训与开发
精益活动倡导和激励机制
精益技术的研究和开发
第三块信息交流是指定期会议,指标体系,目视化管理等等。目的主要是对改善活动的效果进行数目字管理和最佳精益实践的分享。让员工感受到精益活动无处不在,精益就是日常工作的一部分。
另一方面,精益的领导力是指导精益推行的顺利进行和实现预期效果的能力,它也包括两大方面其一是各个层级的目标设定,其二是各个层级的实施计划。
总之,精益的成功实施首先要有精益的领导力,它指明方向和目标;其次要有精益活动的管理,它是保证精益成功的执行力;最后才是精益的方法和工具,它是解决具体问题的法宝。现实中很多人推行精益只讲精益生产的方法和工具,而忽略另二个更重要的因素,失败的可能性当然就很大了。
问二、实施精益就要实行看板拉动吗?
答:这是一个误区,实施精益的主要目的是为了减少浪费,并不一定就要实施拉动的,甚至有些情况是不可能实现拉动的。
一个企业的盈利水平的提高可以通过两种方式实现,一个是加法:在投入不增加的情况下增加产出;一个是减法:在产出不增加的情况下减少投入。当然加法和减法是可以同时做的。
实施精益减少浪费是在做减法,在同等产出下,减少各种的投入。我们常要说拉动,拉动可以有效地减少生产过量的浪费,在某些行业尤其是汽车行业,生产过量是最大的浪费,所以实施拉动,尤其是看板拉动系统是这类行业的常用手法。
但实施精益并不一定要实行拉动系统,拉动系统针对产品型号固定,需求比较稳定,也就是重复性生产的情况下才适用的。很多行业,如牛奶、钢铁等各个工序本身就已是连续流了,还有一些客户定制产品的行业,如机械装备,道路机械等,产品是按客户定制,没有标准化的产品,即使有需求也是比较少量,平均一星期、甚至一个月才出一个同类产品时,拉动是相当难实现的。这种行业型态的浪费表现形式是不一样的,这种情况下实施精益所用的手法就要有所不同,可以从OEE、等待浪费以及质量的浪费的角度去开展改善活动,而不是硬上拉动系统了。这个我称之为生产策略的选择,是对生产模式进行最优定位,有的企业产品需求经过分析后,可能会要几种模式共用的,有的用拉动方法,有的用推动方式生产,有的按库存生产。生产策略的选择有个很好的方法,即ABC/XYZ分析。
问三、精益生产是不是比较适合流水线作业,或者说类同于流水线作业,目前我们公司生产各工序生产作业比较独立,经常会出现很多在制品,产品从投入到产出周期长,我们应该采用流水线作业吗?
答:精益生产没有说只适合流水作业的,精益生产管理的原则是可以用在制造业,服务业的、政府部门,这在国外尤其是日本有很多成功实践的。对于生产各工序生产作业比较独立,经常会出现很多在制品的情况,这里通常的原因就是同步化生产没做好。一个工厂或者一人车间的产出取决于一两个瓶颈工序而已。当他的前工序有生产过量的现象,在制品就会出现,尤其当瓶颈工序有不稳定的现象如设备故障、质量、换型时间过长时,就更会人为地去增加生产在制来避免产能损失。这时就会出现生产在制多,但交期还是没法保证,产品从投入到产出周期长的现象。
免责声明:本文系转载,版权归原作者所有。新益为|精益管理视野鼓励原创行为,本文因转载众多无法找到原作者。如涉及版权,请联系电话023-67015863进行删除!
问一、推动实施精益成功的企业并不多,如何才能提高成功率?
答:推行精益是个系统的工程,要成功地推行精益首先要从万里高空去俯瞰这个企业的问题。推行精益实际是个生产方式重新架构的问题,我们常说TPS是丰田生产方式或者丰田生产系统,就是把它看成一个系统的。所以一个企业要推行精益时首先要回答这个问题,你的生产系统需要什么样的变化才能让你这个企业在质量,成本,交期上有着质的提高。推行精益生产培训和咨询活动成功的标志也是是否让你这个企业成为同行“最佳公司”之一。
从多年推行精益的实践上来看,我认为推行精益的成功要素主要有三点。
精益的方法和工具
精益活动的管理
精益的领导力。
这三点是有层次关系的,从1到3是从下往上的关系。
精益的方法和工具。最常见的就是TPS屋,很多人就把它当成整个丰田生产方式的了,其实这是有误区的,它只解释了丰田生产方式技术上的架构,也可以之为硬件结构。推行精益成功的另两个更重要的要素:改善活动的管理和领导力却没提及。
精益活动的管理本身也包括三大块:1是推动精益的组织结构,2是精益活动的组织和管理,3是信息交流。第一块:改善的组织结构与相应的职能可参见下客户例:
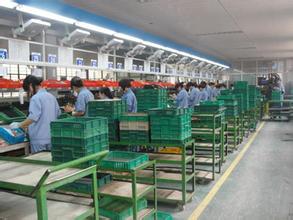
员工精益知识和技能的培训与开发
精益活动倡导和激励机制
精益技术的研究和开发
第三块信息交流是指定期会议,指标体系,目视化管理等等。目的主要是对改善活动的效果进行数目字管理和最佳精益实践的分享。让员工感受到精益活动无处不在,精益就是日常工作的一部分。
另一方面,精益的领导力是指导精益推行的顺利进行和实现预期效果的能力,它也包括两大方面其一是各个层级的目标设定,其二是各个层级的实施计划。
总之,精益的成功实施首先要有精益的领导力,它指明方向和目标;其次要有精益活动的管理,它是保证精益成功的执行力;最后才是精益的方法和工具,它是解决具体问题的法宝。现实中很多人推行精益只讲精益生产的方法和工具,而忽略另二个更重要的因素,失败的可能性当然就很大了。
问二、实施精益就要实行看板拉动吗?
答:这是一个误区,实施精益的主要目的是为了减少浪费,并不一定就要实施拉动的,甚至有些情况是不可能实现拉动的。
一个企业的盈利水平的提高可以通过两种方式实现,一个是加法:在投入不增加的情况下增加产出;一个是减法:在产出不增加的情况下减少投入。当然加法和减法是可以同时做的。
实施精益减少浪费是在做减法,在同等产出下,减少各种的投入。我们常要说拉动,拉动可以有效地减少生产过量的浪费,在某些行业尤其是汽车行业,生产过量是最大的浪费,所以实施拉动,尤其是看板拉动系统是这类行业的常用手法。
但实施精益并不一定要实行拉动系统,拉动系统针对产品型号固定,需求比较稳定,也就是重复性生产的情况下才适用的。很多行业,如牛奶、钢铁等各个工序本身就已是连续流了,还有一些客户定制产品的行业,如机械装备,道路机械等,产品是按客户定制,没有标准化的产品,即使有需求也是比较少量,平均一星期、甚至一个月才出一个同类产品时,拉动是相当难实现的。这种行业型态的浪费表现形式是不一样的,这种情况下实施精益所用的手法就要有所不同,可以从OEE、等待浪费以及质量的浪费的角度去开展改善活动,而不是硬上拉动系统了。这个我称之为生产策略的选择,是对生产模式进行最优定位,有的企业产品需求经过分析后,可能会要几种模式共用的,有的用拉动方法,有的用推动方式生产,有的按库存生产。生产策略的选择有个很好的方法,即ABC/XYZ分析。
问三、精益生产是不是比较适合流水线作业,或者说类同于流水线作业,目前我们公司生产各工序生产作业比较独立,经常会出现很多在制品,产品从投入到产出周期长,我们应该采用流水线作业吗?
答:精益生产没有说只适合流水作业的,精益生产管理的原则是可以用在制造业,服务业的、政府部门,这在国外尤其是日本有很多成功实践的。对于生产各工序生产作业比较独立,经常会出现很多在制品的情况,这里通常的原因就是同步化生产没做好。一个工厂或者一人车间的产出取决于一两个瓶颈工序而已。当他的前工序有生产过量的现象,在制品就会出现,尤其当瓶颈工序有不稳定的现象如设备故障、质量、换型时间过长时,就更会人为地去增加生产在制来避免产能损失。这时就会出现生产在制多,但交期还是没法保证,产品从投入到产出周期长的现象。
免责声明:本文系转载,版权归原作者所有。新益为|精益管理视野鼓励原创行为,本文因转载众多无法找到原作者。如涉及版权,请联系电话023-67015863进行删除!