单件小批制造模式下的精益生产
来源/作者:未知 发布时间:2014年06月18日 阅读次数:次
精益生产意味着速度,时间是制造业流程上最重要、最宝贵的资源,所有的利益都与材料流和信息流的速度成正比
精益生产方式,最早引起人们的注意是在1973年的中东战争导致的石油危机,使完全依赖石油进口的日本经济一落前丈,而丰田的赢利却逐年增加,精益生产方式开始引起人们的注意。
无独有偶,目前的世界经济又出现了由于能源和资源价格上涨而出现的滞涨,企业成本压力越来越大,制造型企业的出路到底在哪里呢?
精益生产方式理念产生于汽车行业,并创造了世界汽车行业的辉煌,丰田汽车,其一家的利润,已超过美国三大汽车公司的总和,它为什么能一贯维持高品质,销售业绩稳定增长,稳定的获利能力,庞大的库存现金。如此骄人的成绩背后,到底有什么秘密呢?
目前,精益生产方式已经从一种生产方式发展、升华为一种优秀的管理理念和文化,对各个行业乃至整个社会产生了巨大的影响。通过"持续改进,消除浪费",实现"以最少的资源,获取最大收益"是精益生产方式的核心思想,也是每个优秀企业不懈的追求。推行精益生产方式是提升企业竞争优势,打造高效率、高品质、高可靠性的强者的必由之路。
作为专业的精益生产咨询机构,十年来专注于各行业的精益生产咨询,所涉及的行业从传统的汽车、电子、机械制造业,到化工、食品、服装等行业,生产模式也从批量制造型到单件小批为特点的行业等,帮助上百家企业成功导入精益生产,辅导过上千家企业的精益生产实施,本文是从单件小批制造型企业的精益生产实施特点着手,与大家共同研讨,谈谈体会与看法。
一、精益生产方式的发展及其推广应用情况
精益生产方式方式是一种以最大限度地减少生产所占用的资源,降低企业管理和运营成本,高质量、高可靠性、准时交付为主要目标的生产方式。依靠精益生产方式,日本汽车工业于80年代初实现了赶超美国的目标。90年代美国人学习、应用精益生产方式管理理论给世界汽车工业带来了巨大的变革,目前,精益生产管理已在机械、电子、消费品、航空、航天、造船工业中广泛应用,几乎全世界知名的制造业都实践了精益生产方式理论并从中获得了丰厚的回报。
沈阳鼓风机集团作为装备制造业的典型代表,具有鲜明的单件小批制造模式的特点,他们率先作出尝试,将这种起步于丰田,并伴随丰田成长壮大,又被全世各行业所实践的精益生产方式引进来,结合自身的特点,勇于实践,并初步取得效果,作为与之合作的咨询公司,也有一些体会与大家分享,以期对此类企业的精益生产推行起到启发作用。
二、单件小批制造业的特点
1.非通用型产品,只有接订单后,获知客户要求后方能设计和生产,通常客户要求各异
2.不同的产品有各自的工艺加工路线,加工时间各不相同
三、单件小批制造模式的生产运作通用问题
1.准时交货表现差
由于是个性化,按客户要求设计、制造的产品,导致设计、工艺的标准化程度很低,没有经验证确定的产品加工工艺路线和加工时间,导致生产计划在排程时对产品制造周期把握不准确,从而无法确定准确的完成时间;
2.在制品多,制造周期长
无法确定准确的投料时间,认为越早投入越安全,从而存在过早投料的现象,导致流程中物料过多
3.齐套性不好
采购和各自制配套件的准时化提供程度很低,缺件现象严重
四、某企业的实际生产运作表现
1.公司当前的准时交付率很低
-30%的订单能准时交付,50%的订单迟交付但延迟时间不长,其余20%延期超过三个月以上;
2.公司对客户造成的损失
-许多公司依靠这家公司的产品,成为客户产品的关键零部件和生产设备,会引起客户生产中断,导致每天几百万元的损失
3.公司制造周期太长,没有被市场认为是一个可靠的供应商
-市场由于缺乏同类型产品的产能,客户推动该公司每年接受了更多的订单.由于关键资源所限,等待时间加长,导致产品的制造周期加长.
急单处理
-生产由于不断的更换优先顺序受到冲击,一边是花费了很多的努力和时间,一边是带来了生产流程的中断.
质量问题
-由于经常赶延期订单,导致生产人员经常面对临时改变的流程,这通常导致在后端组装工序发现质量问题,从而无法对其根源进行确定
库存太高,资金紧张,利润偏低
-存货资金周转次数小于2次/年,,净利润只有2%
免责声明:本文系转载,版权归原作者所有。新益为|精益管理视野鼓励原创行为,本文因转载众多无法找到原作者。如涉及版权,请联系电话023-67015863进行删除!
精益生产方式,最早引起人们的注意是在1973年的中东战争导致的石油危机,使完全依赖石油进口的日本经济一落前丈,而丰田的赢利却逐年增加,精益生产方式开始引起人们的注意。
无独有偶,目前的世界经济又出现了由于能源和资源价格上涨而出现的滞涨,企业成本压力越来越大,制造型企业的出路到底在哪里呢?
精益生产方式理念产生于汽车行业,并创造了世界汽车行业的辉煌,丰田汽车,其一家的利润,已超过美国三大汽车公司的总和,它为什么能一贯维持高品质,销售业绩稳定增长,稳定的获利能力,庞大的库存现金。如此骄人的成绩背后,到底有什么秘密呢?
目前,精益生产方式已经从一种生产方式发展、升华为一种优秀的管理理念和文化,对各个行业乃至整个社会产生了巨大的影响。通过"持续改进,消除浪费",实现"以最少的资源,获取最大收益"是精益生产方式的核心思想,也是每个优秀企业不懈的追求。推行精益生产方式是提升企业竞争优势,打造高效率、高品质、高可靠性的强者的必由之路。
作为专业的精益生产咨询机构,十年来专注于各行业的精益生产咨询,所涉及的行业从传统的汽车、电子、机械制造业,到化工、食品、服装等行业,生产模式也从批量制造型到单件小批为特点的行业等,帮助上百家企业成功导入精益生产,辅导过上千家企业的精益生产实施,本文是从单件小批制造型企业的精益生产实施特点着手,与大家共同研讨,谈谈体会与看法。
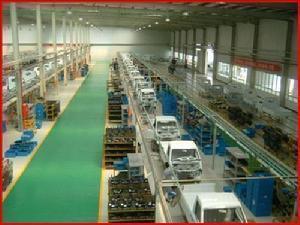
精益生产方式方式是一种以最大限度地减少生产所占用的资源,降低企业管理和运营成本,高质量、高可靠性、准时交付为主要目标的生产方式。依靠精益生产方式,日本汽车工业于80年代初实现了赶超美国的目标。90年代美国人学习、应用精益生产方式管理理论给世界汽车工业带来了巨大的变革,目前,精益生产管理已在机械、电子、消费品、航空、航天、造船工业中广泛应用,几乎全世界知名的制造业都实践了精益生产方式理论并从中获得了丰厚的回报。
沈阳鼓风机集团作为装备制造业的典型代表,具有鲜明的单件小批制造模式的特点,他们率先作出尝试,将这种起步于丰田,并伴随丰田成长壮大,又被全世各行业所实践的精益生产方式引进来,结合自身的特点,勇于实践,并初步取得效果,作为与之合作的咨询公司,也有一些体会与大家分享,以期对此类企业的精益生产推行起到启发作用。
二、单件小批制造业的特点
1.非通用型产品,只有接订单后,获知客户要求后方能设计和生产,通常客户要求各异
2.不同的产品有各自的工艺加工路线,加工时间各不相同
三、单件小批制造模式的生产运作通用问题
1.准时交货表现差
由于是个性化,按客户要求设计、制造的产品,导致设计、工艺的标准化程度很低,没有经验证确定的产品加工工艺路线和加工时间,导致生产计划在排程时对产品制造周期把握不准确,从而无法确定准确的完成时间;
2.在制品多,制造周期长
无法确定准确的投料时间,认为越早投入越安全,从而存在过早投料的现象,导致流程中物料过多
3.齐套性不好
采购和各自制配套件的准时化提供程度很低,缺件现象严重
四、某企业的实际生产运作表现
1.公司当前的准时交付率很低
-30%的订单能准时交付,50%的订单迟交付但延迟时间不长,其余20%延期超过三个月以上;
2.公司对客户造成的损失
-许多公司依靠这家公司的产品,成为客户产品的关键零部件和生产设备,会引起客户生产中断,导致每天几百万元的损失
3.公司制造周期太长,没有被市场认为是一个可靠的供应商
-市场由于缺乏同类型产品的产能,客户推动该公司每年接受了更多的订单.由于关键资源所限,等待时间加长,导致产品的制造周期加长.
急单处理
-生产由于不断的更换优先顺序受到冲击,一边是花费了很多的努力和时间,一边是带来了生产流程的中断.
质量问题
-由于经常赶延期订单,导致生产人员经常面对临时改变的流程,这通常导致在后端组装工序发现质量问题,从而无法对其根源进行确定
库存太高,资金紧张,利润偏低
-存货资金周转次数小于2次/年,,净利润只有2%
免责声明:本文系转载,版权归原作者所有。新益为|精益管理视野鼓励原创行为,本文因转载众多无法找到原作者。如涉及版权,请联系电话023-67015863进行删除!