精益生产管理技术
来源/作者:未知 发布时间:2013年07月09日 阅读次数:次
精益生产思想随着近几年的不断发展,已经渗透到社会的各个层面,各行各业都可以运用精益生产思想不断的发展。目前精益生产管理思想也是管理顾问和管理咨询师关注的问题,许多管理顾问和管理咨询师都在不断的研究精益生产管理思想,使其更能适应企业的发展。
精益生产管理的思想主要有五个方面:1)精确地确定特定产品的价值;2)识别每种产品的价值流;3)使价值不断地流动;4)让用户从生产者方面拉动价值;5)永远追求尽善尽美。
确定价值。精益生产思想的关键出发点是价值。价值只能由最终用户来确定,而价值也只有由具有特定价格、能在特定时间内满足用户需求的特定产品(商品或服务,而经常是既是商品又是服务的产品)来表达时才有意义。价值是由生产者创造的,从用户的立场来看,这是生产者之所以存在的理由。
价值的定义被现存的组织、技术、未折旧的资产的力量、以及过了时的规模经济的思想歪曲了。世界各地的管理人员都爱说“我们知道如何利用已经买到的材料和设备来生产这种产品。如果用户不接受,我们可以调整价格,或者增加一些装饰品。”绩效管理而实际上他们真正要做的是站在用户的立场上从根本上重新思考价值。遗憾的是随着技术的发展,现代人单纯为了绩效管理技术的实现而从事经营生产,产品的生产者越来越脱离用户,一些用户不需求的功能硬性强加,造成资源的惊人浪费。
识别价值流。价值流是使一个特定产品(不论上一个商品、一项服务,或者商品和服务两者的结合)通过任何一项商务活动的三项关键性管理任务时所必须的一组特定活动。这三项任务是:在从概念设想,通过细节设计与工程,到投产可持续发展的全过程中解决问题的任务;在从接订单到制定详细进度到送货的全过程中的信息管理任务;在从原材料制成最终产品,送到用户手中的物质转化任务。确定每个产品的全部价值流是精益生产思想的第二步。虽然企业很少注意到这一步,但是这一阶段通常会暴露出大量的、错综复杂的浪费。
价值流分析几乎总能显示出沿价值流的三种活动方式:1)有很多明确的能创造价值的步骤;2)有很多虽然不创造价值,但是在现有技术与生产条件下不可避免的其他步骤;3)还有很多不创造价值而且可以立即去掉的步骤。
精益生产思想必须超出企业这个世界上公认的划分单位的标准,去查看创造和生产一个特定产品所必须的全部活动。这些活动包括从概念经过细节设计到实际可用的产品,从开始销售经过接受订单、计划生产到送货,可持续生产以及从远方生产的原材料到将产品交到用户手中的全部活动。我们把完成所有这些事情的组织机构成为精益企业。形成精益企业确实需要用新的方法去思考企业与企业间的关系,需要一些简单原则来规范企业间的行为,管理培训以及沿价值流的所有步骤的透明度。
流动。一旦精确地确定了价值,精益企业也完整地制定出了某一特定产品的价值流程图,消灭了明显的浪费步骤,实行精益生产思想中的第三步也就到了。这才是真正精彩的阶段:管理培训要使保留下来的、创造价值的各个步骤流动起来。但是请特别注意,这一步要求你完全更新自己的思想。
我们生存在一个认同“职能”与“部门”的世界里,也就是说大家都认为,各种活动都应该按类型分组,以便能有效地运做也易于管理。这种方法使部门人员忙个不停,使所有的设备用得很苦,而且需要使用精密的高速设备。实际上这是极其错误的,但是我们中的大多数人很难意识到这一点,或者根本没意识到这一点。
大野耐一把主张成批与排队的思想模式归罪于人类文明中最早的农民。他认为,是这些人在进行成批生产(一年一度的农作物收获)和储存(收粮入仓)的过程中,丢掉了猎人们那种一物一猎的明智。或者我们的头脑中也许生来就有了成批生产的概念和许多其他错误“常识”。我们所有的人必须和部门化、批量生产的思想作斗争,因为如果产品按从原材料到成品的过程连续来生产的话,我们的工作几乎总能完成得有效而精确得多。当你把精力放在产品和产品的需要上,而不是放在组织或设备上时,事情就会办得好一些。因此所有为设计、订货和提供产品所需要的活动应该在连续的流动中进行。
亨利福特和他的助手们是最先真正认识到流动潜力的人。1913年秋,福特把汽车的最后总装转变为连续流动的方式,使福特T型车的总装工作量减少了90%。接着他把生产T型车零件的所有机床按照正确的顺序排列起来,并且试着使从原材料到成品车发货的整个过程流动起来,由此也同样大大提高了生产率。但是,他只是发现了特例。他的方法只能在生产量大到必须使用高速装配线才能完成,每个产品都使用完全相同的零件、同一车型要持续生产很多年。
第二次世界大战后,大野耐一和他的技术人员得出了结论,真正的挑战是在少量生产时创造连续流动。这时一种产品只要生产几十个或几百个。大野和他的同事们实现了在少量生产条件下的连续流动,在大多数情况下不用装配线,而是学习迅速调整工装,从一种产品转产到另一种产品,并且使用小型化的机床,这样不同类型的工艺步骤可以马上相互调整,以使正在进行的加工保持在连续的流动中。
精益的方法是要重新定义职能、部门和企业的作用,使它们能对创造价值作出积极的贡献;是要说明价值流上每一点的员工的真正需要,因此,使价值流动起来才真正符合员工的利益。这不仅要求为每种产品建立精益企业,还应该重新思考传统的企业、职能、职业,重新考虑精益战略的发展。
拉动。从“部门”和“批量”转化到“生产团队”和“流动”,第一个可见效果是:从概念到投产、销售到送货以及原材料到用户所需的时间大大地减少了。引进了流动以后,需要几年才能设计出来的产品,在几个月内就可以完成;需要若干天才能办完的订货手续几个小时就可办完。传统的物质生产时间由几周或几个月减少到几天或几分钟。实际上,如果你不能迅速地把产品开发时间减半、订货时间减少75%、生产时间减少90%,那你一定是哪儿做错了。而且精益系统现在可以使正在生产的所有产品进行任意组合,所以变化了的需求可以及时得到满足。
这种做法能从库存量下降和投资回收速度加快中一下子节省大量现金,它的确是个革命性的成就。因为,一旦有了在用户需要的时候就能设计、安排生产和制造出用户真正需要的产品的能力,就意味着你可以抛开销售预测,直接按用户告诉你的实际要求生产就行了。这就是说,你可以让用户从你那里按需求拉动产品,而不是把用户常常不想要的产品硬推给用户。当用户知道他们可以立刻得到他们所要的东西时,而且当生产者停止定期的减价销售活动,不再把已经生产出来却没人要的产品推销出去时,用户的需求就变得稳定多了。
尽善尽美。当各种组织开始精确地确定价值、识别出整个价值流、使得为特定产品创造价值的各个步骤连续流动起来,并且让用户从企业拉动价值时,奇迹就开始出现了。他表现为在提供出一个比以往更接近用户真正需要的产品时,人们也在无止境地不断减少付出的努力、时间、场地、成本和错误。突然之间,尽善尽美这个精益生产思想的第五个原则看起来就不像是一种胡思乱想了。
为什么会是这样呢?因为上述四个原则在良性循环中相互作用,让价值流动得快一些总能暴露出价值流隐藏的浪费。你越是使劲拉动,阻碍流动的障碍就会显现出来,从而也就能将它们排除。专职产品工作团队直接与用户对话,总能更精确地确定价值,并且也常常能学到增进流动和拉动的各种方法。 免责声明:本文系转载,版权归原作者所有。新益为|精益管理视野鼓励原创行为,本文因转载众多无法找到原作者。如涉及版权,请联系电话023-67015863进行删除!
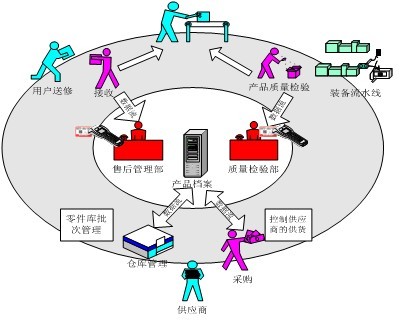
精益生产管理的思想主要有五个方面:1)精确地确定特定产品的价值;2)识别每种产品的价值流;3)使价值不断地流动;4)让用户从生产者方面拉动价值;5)永远追求尽善尽美。
确定价值。精益生产思想的关键出发点是价值。价值只能由最终用户来确定,而价值也只有由具有特定价格、能在特定时间内满足用户需求的特定产品(商品或服务,而经常是既是商品又是服务的产品)来表达时才有意义。价值是由生产者创造的,从用户的立场来看,这是生产者之所以存在的理由。
价值的定义被现存的组织、技术、未折旧的资产的力量、以及过了时的规模经济的思想歪曲了。世界各地的管理人员都爱说“我们知道如何利用已经买到的材料和设备来生产这种产品。如果用户不接受,我们可以调整价格,或者增加一些装饰品。”绩效管理而实际上他们真正要做的是站在用户的立场上从根本上重新思考价值。遗憾的是随着技术的发展,现代人单纯为了绩效管理技术的实现而从事经营生产,产品的生产者越来越脱离用户,一些用户不需求的功能硬性强加,造成资源的惊人浪费。
识别价值流。价值流是使一个特定产品(不论上一个商品、一项服务,或者商品和服务两者的结合)通过任何一项商务活动的三项关键性管理任务时所必须的一组特定活动。这三项任务是:在从概念设想,通过细节设计与工程,到投产可持续发展的全过程中解决问题的任务;在从接订单到制定详细进度到送货的全过程中的信息管理任务;在从原材料制成最终产品,送到用户手中的物质转化任务。确定每个产品的全部价值流是精益生产思想的第二步。虽然企业很少注意到这一步,但是这一阶段通常会暴露出大量的、错综复杂的浪费。
价值流分析几乎总能显示出沿价值流的三种活动方式:1)有很多明确的能创造价值的步骤;2)有很多虽然不创造价值,但是在现有技术与生产条件下不可避免的其他步骤;3)还有很多不创造价值而且可以立即去掉的步骤。
精益生产思想必须超出企业这个世界上公认的划分单位的标准,去查看创造和生产一个特定产品所必须的全部活动。这些活动包括从概念经过细节设计到实际可用的产品,从开始销售经过接受订单、计划生产到送货,可持续生产以及从远方生产的原材料到将产品交到用户手中的全部活动。我们把完成所有这些事情的组织机构成为精益企业。形成精益企业确实需要用新的方法去思考企业与企业间的关系,需要一些简单原则来规范企业间的行为,管理培训以及沿价值流的所有步骤的透明度。
流动。一旦精确地确定了价值,精益企业也完整地制定出了某一特定产品的价值流程图,消灭了明显的浪费步骤,实行精益生产思想中的第三步也就到了。这才是真正精彩的阶段:管理培训要使保留下来的、创造价值的各个步骤流动起来。但是请特别注意,这一步要求你完全更新自己的思想。
我们生存在一个认同“职能”与“部门”的世界里,也就是说大家都认为,各种活动都应该按类型分组,以便能有效地运做也易于管理。这种方法使部门人员忙个不停,使所有的设备用得很苦,而且需要使用精密的高速设备。实际上这是极其错误的,但是我们中的大多数人很难意识到这一点,或者根本没意识到这一点。
大野耐一把主张成批与排队的思想模式归罪于人类文明中最早的农民。他认为,是这些人在进行成批生产(一年一度的农作物收获)和储存(收粮入仓)的过程中,丢掉了猎人们那种一物一猎的明智。或者我们的头脑中也许生来就有了成批生产的概念和许多其他错误“常识”。我们所有的人必须和部门化、批量生产的思想作斗争,因为如果产品按从原材料到成品的过程连续来生产的话,我们的工作几乎总能完成得有效而精确得多。当你把精力放在产品和产品的需要上,而不是放在组织或设备上时,事情就会办得好一些。因此所有为设计、订货和提供产品所需要的活动应该在连续的流动中进行。
亨利福特和他的助手们是最先真正认识到流动潜力的人。1913年秋,福特把汽车的最后总装转变为连续流动的方式,使福特T型车的总装工作量减少了90%。接着他把生产T型车零件的所有机床按照正确的顺序排列起来,并且试着使从原材料到成品车发货的整个过程流动起来,由此也同样大大提高了生产率。但是,他只是发现了特例。他的方法只能在生产量大到必须使用高速装配线才能完成,每个产品都使用完全相同的零件、同一车型要持续生产很多年。
第二次世界大战后,大野耐一和他的技术人员得出了结论,真正的挑战是在少量生产时创造连续流动。这时一种产品只要生产几十个或几百个。大野和他的同事们实现了在少量生产条件下的连续流动,在大多数情况下不用装配线,而是学习迅速调整工装,从一种产品转产到另一种产品,并且使用小型化的机床,这样不同类型的工艺步骤可以马上相互调整,以使正在进行的加工保持在连续的流动中。
精益的方法是要重新定义职能、部门和企业的作用,使它们能对创造价值作出积极的贡献;是要说明价值流上每一点的员工的真正需要,因此,使价值流动起来才真正符合员工的利益。这不仅要求为每种产品建立精益企业,还应该重新思考传统的企业、职能、职业,重新考虑精益战略的发展。
拉动。从“部门”和“批量”转化到“生产团队”和“流动”,第一个可见效果是:从概念到投产、销售到送货以及原材料到用户所需的时间大大地减少了。引进了流动以后,需要几年才能设计出来的产品,在几个月内就可以完成;需要若干天才能办完的订货手续几个小时就可办完。传统的物质生产时间由几周或几个月减少到几天或几分钟。实际上,如果你不能迅速地把产品开发时间减半、订货时间减少75%、生产时间减少90%,那你一定是哪儿做错了。而且精益系统现在可以使正在生产的所有产品进行任意组合,所以变化了的需求可以及时得到满足。
这种做法能从库存量下降和投资回收速度加快中一下子节省大量现金,它的确是个革命性的成就。因为,一旦有了在用户需要的时候就能设计、安排生产和制造出用户真正需要的产品的能力,就意味着你可以抛开销售预测,直接按用户告诉你的实际要求生产就行了。这就是说,你可以让用户从你那里按需求拉动产品,而不是把用户常常不想要的产品硬推给用户。当用户知道他们可以立刻得到他们所要的东西时,而且当生产者停止定期的减价销售活动,不再把已经生产出来却没人要的产品推销出去时,用户的需求就变得稳定多了。
尽善尽美。当各种组织开始精确地确定价值、识别出整个价值流、使得为特定产品创造价值的各个步骤连续流动起来,并且让用户从企业拉动价值时,奇迹就开始出现了。他表现为在提供出一个比以往更接近用户真正需要的产品时,人们也在无止境地不断减少付出的努力、时间、场地、成本和错误。突然之间,尽善尽美这个精益生产思想的第五个原则看起来就不像是一种胡思乱想了。
为什么会是这样呢?因为上述四个原则在良性循环中相互作用,让价值流动得快一些总能暴露出价值流隐藏的浪费。你越是使劲拉动,阻碍流动的障碍就会显现出来,从而也就能将它们排除。专职产品工作团队直接与用户对话,总能更精确地确定价值,并且也常常能学到增进流动和拉动的各种方法。 免责声明:本文系转载,版权归原作者所有。新益为|精益管理视野鼓励原创行为,本文因转载众多无法找到原作者。如涉及版权,请联系电话023-67015863进行删除!